Ultralong unit extension glass fiber reinforced polypropylene composite material
A technology of glass fiber and composite materials, which is applied in the field of preparation of ultra-long elongation glass fiber reinforced polypropylene composite materials, can solve the problems of high strength, rigidity and heat resistance, cannot be bent multiple times, and is brittle. Achieve excellent physical and mechanical properties and reduce costs
- Summary
- Abstract
- Description
- Claims
- Application Information
AI Technical Summary
Problems solved by technology
Method used
Image
Examples
Embodiment 1~4
[0028] The weight percentages of various raw materials in the composite material are shown in Table 1. The temperatures of the twin-screw extruder are (from the feeding port to the extrusion die): 170°C, 190°C, 215°C, 230°C, 235°C . The host speed is 30 Hz.
[0029] Table 1 Example 1-4 formula and material performance table
[0030]
[0031]
Embodiment 5~7
[0033] The weight percentages of various raw materials in the composite material are shown in Table 2. The temperatures of the twin-screw extruder are (from the feeding port to the extrusion die): 170°C, 190°C, 215°C, 230°C, 235°C . The host speed is 30 Hz.
[0034] Table 2 Example 5-7 formula and material performance table
[0035]
Embodiment 8~11
[0037] The weight percentages of various raw materials in the composite material are shown in Table 3. The temperatures of the twin-screw extruder are (from the feeding port to the extrusion die): 170°C, 190°C, 215°C, 230°C, 235°C . The host speed is 30 Hz.
[0038] Table 3 Example 8-11 formula and material performance table
[0039]
PUM
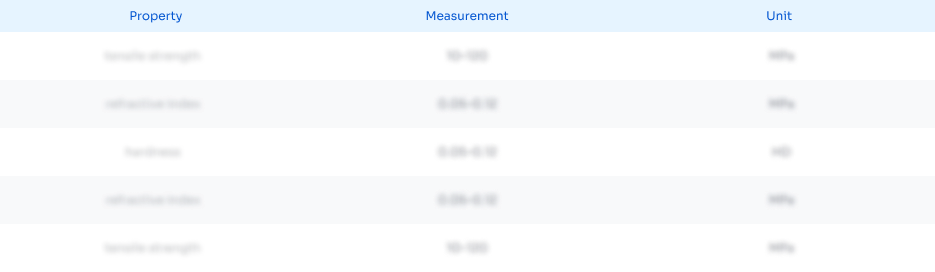
Abstract
Description
Claims
Application Information

- R&D
- Intellectual Property
- Life Sciences
- Materials
- Tech Scout
- Unparalleled Data Quality
- Higher Quality Content
- 60% Fewer Hallucinations
Browse by: Latest US Patents, China's latest patents, Technical Efficacy Thesaurus, Application Domain, Technology Topic, Popular Technical Reports.
© 2025 PatSnap. All rights reserved.Legal|Privacy policy|Modern Slavery Act Transparency Statement|Sitemap|About US| Contact US: help@patsnap.com