Manufacture technique of detoxicated rapeseed protein powder as feedstuff
A manufacturing process and technology of protein powder, which is applied in the molding or processing of animal feed, animal feed, animal feed, etc., can solve the problem that the detoxification effect is greatly affected by the environment, cannot remove phytate and tannin, and occupies a large area. and other problems, to achieve the effect of good detoxification effect, environmental protection and low production cost.
- Summary
- Abstract
- Description
- Claims
- Application Information
AI Technical Summary
Problems solved by technology
Method used
Examples
Embodiment 1
[0031] A kind of specific method step of the detoxified concentrated rapeseed protein powder manufacturing process for feed is as follows:
[0032] (1) Initial detoxification by medium pressure steam
[0033] The defatted rapeseed meal after leaching rapeseed oil is used as the raw material, first crushed by a grinder and passed through a 20-mesh screen, and those that have not passed the screen are returned to the grinder and crushed again. The powder passing through the sieve is collected to prepare defatted rapeseed meal powder. Then according to the weight of defatted rapeseed meal powder: the ratio of soft water volume ratio is 1: 0.5, add soft water in the defatted rapeseed meal powder, place on 100 mesh screens after stirring evenly, then place it in the bottom filled with water In the high-pressure vessel, the water level is below the screen on which the defatted rapeseed meal is placed. After sealing, heat up to the water at the bottom of the high-pressure container...
Embodiment 2
[0048] A kind of specific method step of the detoxified concentrated rapeseed protein powder manufacturing process for feed is as follows:
[0049] (1) Initial detoxification by medium pressure steam
[0050] With embodiment 1, it is characterized in that: according to the weight of defatted rapeseed meal powder: soft water volume ratio is 1: 0.6, water vapor pressure is 0.5Mpa, keeps 60 minutes under constant pressure condition.
[0051] (2) Solution detoxification
[0052] ① Preparation of detoxification extract
[0053] With embodiment 1, it is characterized in that: soft water: the volume ratio of concentrated hydrochloric acid is 100:2.
[0054] ②Dilute hydrochloric acid solution detoxification and separation
[0055] Same as Example 1, characterized in that: the mass of preliminary detoxified rapeseed dregs: the volume ratio of the detoxified extract is 1:5, the temperature is raised to 40° C. under stirring, and the temperature is maintained for 45 minutes. Then the...
Embodiment 3
[0063] A kind of specific method step of the detoxified concentrated rapeseed protein powder manufacturing process for feed is as follows:
[0064] (1) Initial detoxification by medium pressure steam
[0065] With embodiment 1, it is characterized in that: the weight of defatted rapeseed meal powder: soft water volume ratio is 1: 0.75, and steam pressure is 0.6Mpa, keeps 30 minutes under constant pressure condition.
[0066] (2) Solution detoxification
[0067] ① Preparation of detoxification extract
[0068] With embodiment 1, it is characterized in that: soft water: the volume of concentrated hydrochloric acid is 100: 3.0.
[0069] ②Dilute hydrochloric acid solution detoxification and separation
[0070] Same as Example 1, characterized in that: the mass of preliminary detoxified rapeseed dregs: the volume ratio of the detoxified extract is 1:6, the temperature is raised to 50° C. under stirring, and the temperature is maintained for 30 minutes. The mass of detoxified ra...
PUM
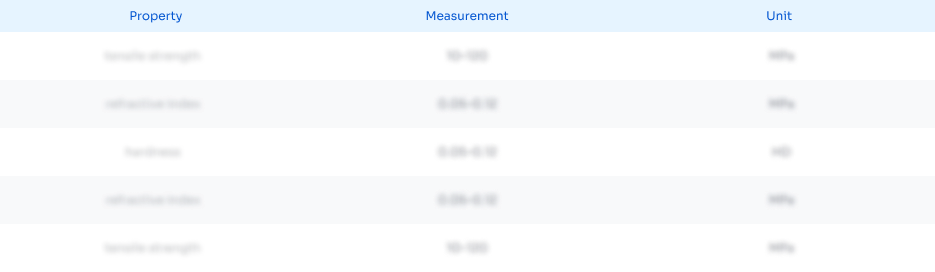
Abstract
Description
Claims
Application Information

- Generate Ideas
- Intellectual Property
- Life Sciences
- Materials
- Tech Scout
- Unparalleled Data Quality
- Higher Quality Content
- 60% Fewer Hallucinations
Browse by: Latest US Patents, China's latest patents, Technical Efficacy Thesaurus, Application Domain, Technology Topic, Popular Technical Reports.
© 2025 PatSnap. All rights reserved.Legal|Privacy policy|Modern Slavery Act Transparency Statement|Sitemap|About US| Contact US: help@patsnap.com