Method for preparing nickel and cobalt doped lithium manganate by using waste and old lithium ionic cell as raw material
A lithium-ion battery, nickel-cobalt lithium manganate technology, applied in the direction of manganate/permanganate, etc., can solve the problem of unsuitable disposal of waste lithium-ion batteries, and achieve high added value of products, short process flow, raw materials low price effect
- Summary
- Abstract
- Description
- Claims
- Application Information
AI Technical Summary
Problems solved by technology
Method used
Image
Examples
Embodiment 1
[0028] After the polymer lithium-ion battery was disassembled, 100 g of the positive electrode sheet was selected and crushed with a vertical high-speed rotary grinder. The crushing time was set at 5 minutes. After crushing, it was sieved with an 80-mesh standard sieve. The total weight of the oversize is 11.3g, and the total weight of the undersize is 88.7g; detected by the atomic absorption instrument, the aluminum content in the oversize is 81.4%, and the total content of nickel, cobalt and manganese is about 5.50%; the aluminum content of the undersize is 0.9%, the cobalt content is 18.5%, the nickel content is 18.0%, and the manganese content is 16.9%. Therefore, the aluminum removal rate is calculated to be 92.0%, and the total loss of nickel, cobalt, and manganese caused by the positive electrode material contained in the aluminum slag on the sieve is 1.3%.
Embodiment 2
[0030]Take 50 g of the undersize in Example 1, put it into a high-temperature electric furnace, keep the air circulation, raise the temperature to 600 ° C, keep the temperature for 4 hours, and the burnt residue weighs 45.1 g. The CS800 infrared carbon and sulfur detector was used to detect that the carbon content was about 0.01%, indicating that the binder and acetylene black were basically completely removed. Take 40g of the burning residue and put it into a 500mL beaker, add 150mL of sodium hydroxide with a concentration of 0.2mol / L, the amount of sodium hydroxide is twice the theoretical value, put the beaker into a constant temperature water bath, and adjust the temperature to 65°C. Keep stirring with a magnetic stirrer, react for 40 minutes, and filter. The obtained filter residue is washed with distilled water several times until it becomes neutral, and then put in an oven and dried at 150°C for 12 hours. After grinding and pulverizing, the waste positive electrode mater...
Embodiment 3
[0032] Get waste positive electrode material 35.0g among the embodiment 2 and put into beaker, add concentration and be the sulfuric acid 210ml of 4.0mol / L, wherein contain 40ml hydrogen peroxide solution (H 2 o 2 content is 30%), put the beaker into a constant temperature water bath, adjust the temperature to 90°C, keep stirring with a magnetic stirrer, after reacting for 60min, filter to remove the filter residue, and set the filtrate to a constant volume of 500ml. EDTA complexometric titration, flame atomic absorption spectrometry and plasma emission spectrometry (ICP) are used to detect the metal element content in the leachate as follows:
[0033]
[0034] After calculation, the leaching rates of nickel, cobalt and manganese are 99.0%, 99.5% and 99.8% in sequence.
PUM
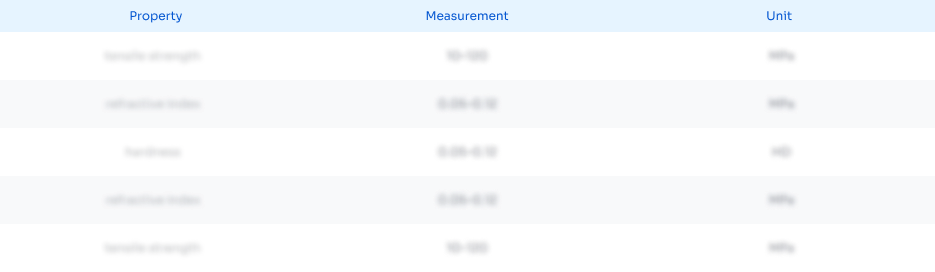
Abstract
Description
Claims
Application Information

- Generate Ideas
- Intellectual Property
- Life Sciences
- Materials
- Tech Scout
- Unparalleled Data Quality
- Higher Quality Content
- 60% Fewer Hallucinations
Browse by: Latest US Patents, China's latest patents, Technical Efficacy Thesaurus, Application Domain, Technology Topic, Popular Technical Reports.
© 2025 PatSnap. All rights reserved.Legal|Privacy policy|Modern Slavery Act Transparency Statement|Sitemap|About US| Contact US: help@patsnap.com