A resource recovery and treatment method for smelting wastewater sedimentation slag
A technology of resource recovery and treatment method, applied in the field of solid waste treatment in the metallurgical industry, can solve the problems of poor adaptability of raw materials, low resource recovery rate, low production efficiency, etc., and achieve the effects of low production cost, simplified purification process and fast response
- Summary
- Abstract
- Description
- Claims
- Application Information
AI Technical Summary
Problems solved by technology
Method used
Image
Examples
Embodiment 1
[0029] The raw material vanadium smelting wastewater sedimentation slag treated in this example is the sedimentation slag produced after the vanadium smelting wastewater is treated by the combined chemical-coagulation process. It is provided by a domestic vanadium smelting enterprise. Its chemical composition is as follows, and the contents of each element are is the mass percent content.
[0030]
[0031] A method for resource recovery and treatment of vanadium smelting wastewater sedimentation slag, specifically including steps:
[0032] S1: crush and finely grind the precipitated slag from vanadium smelting wastewater. The grinding fineness is less than 0.074 mm, accounting for 82%, to obtain precipitated finely ground slag, and then mix the precipitated finely ground slag with sodium carbonate. 30% by weight, and then put it into a microwave muffle furnace for short-term roasting. The microwave conditions are: microwave frequency 2000MHz, microwave power 1500W, and roas...
Embodiment 2
[0037] The raw material vanadium smelting wastewater precipitated slag treated in this embodiment is the same as that in Embodiment 1.
[0038] A method for resource recovery and treatment of vanadium smelting wastewater sedimentation slag, specifically including steps:
[0039]S1: Crushing and finely grinding the vanadium smelting wastewater sedimentation slag, the grinding fineness is less than 0.074 mm, accounting for 83%, to obtain the precipitated fine grinding slag, and then mixing the precipitated fine grinding slag with sodium carbonate, the amount of sodium carbonate added is the vanadium smelting wastewater precipitation slag 40% by weight, and then put it into a microwave muffle furnace for short-term calcination, the microwave conditions are: microwave frequency 900MHz, microwave power 1000W, calcination temperature 600 ℃. The short-term roasting time is controlled to be 50 minutes; the roasted slag is obtained.
[0040] S2: adding water to the calcined slag obtai...
Embodiment 3
[0044] The raw material vanadium smelting wastewater precipitated slag treated in this embodiment is the same as that in Embodiment 1.
[0045] A method for resource recovery and treatment of vanadium smelting wastewater sedimentation slag, specifically including steps:
[0046] S1: crush and finely grind the vanadium smelting wastewater sediment slag, the grinding fineness is less than 0.074 mm, accounting for 85%, to obtain the precipitated fine grinding slag, and then mix the precipitated fine grinding slag with sodium carbonate, and the amount of sodium carbonate added is the vanadium smelting wastewater sediment slag 20% by weight, and then put it into a microwave muffle furnace for short-term calcination. The microwave conditions are: microwave frequency 2500MHz, microwave power 500W, and calcination temperature 400°C. The short-term roasting time is controlled to be 45 minutes; the roasted slag is obtained.
[0047] S2: adding water to the calcined slag obtained in ste...
PUM
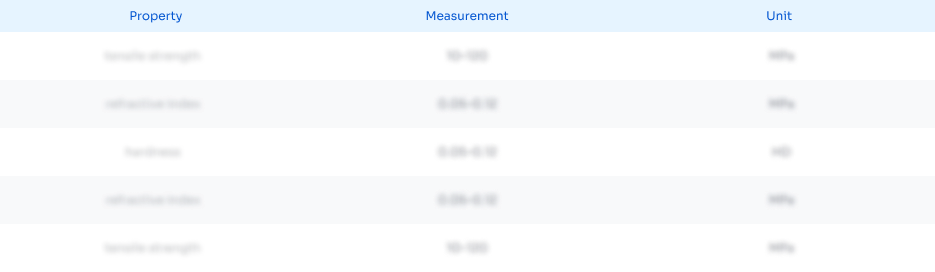
Abstract
Description
Claims
Application Information

- R&D
- Intellectual Property
- Life Sciences
- Materials
- Tech Scout
- Unparalleled Data Quality
- Higher Quality Content
- 60% Fewer Hallucinations
Browse by: Latest US Patents, China's latest patents, Technical Efficacy Thesaurus, Application Domain, Technology Topic, Popular Technical Reports.
© 2025 PatSnap. All rights reserved.Legal|Privacy policy|Modern Slavery Act Transparency Statement|Sitemap|About US| Contact US: help@patsnap.com