Low-temperature steel flux-cored wire
A technology of flux-cored welding wire and low-temperature steel, applied in the direction of welding medium, welding equipment, welding/cutting medium/material, etc., can solve the problems of poor welding process performance, poor arc stability, and high cost, and achieve low-temperature impact toughness and low-temperature resistance Good crack resistance, excellent low temperature impact toughness, high welding efficiency
- Summary
- Abstract
- Description
- Claims
- Application Information
AI Technical Summary
Problems solved by technology
Method used
Examples
Embodiment 1
[0011] The preparation method of the present invention adopts prior art, is manufactured with following process:
[0012] 1. Raw materials for preparing the drug core: rutile, wollastonite, silicon-manganese alloy, iron powder, nickel powder, cryolite, feldspar, ferro-titanium, ferro-boron, medium-carbon ferromanganese, magnesia, quartz and fluorite. Requirements TiO in rutile 2 The content is 96%; CaSiO in wollastonite 3 The content of Ni in silicon-manganese alloy is 67%; Si22% in silicon-manganese alloy, Mn78%; Fe content in iron powder is 98%; Ni content in nickel powder is 99%; Na in cryolite 3 AlF 6 The content is 98%; SiO in feldspar 2 68%, Al 2 o 3 18%; Ti21% in ferro-titanium; B21% in ferroboron; Mn80% in medium carbon ferromanganese; MgO content in magnesia is 98%; SiO in quartz 2 The content is 98%; CaF in fluorite 2 The content is 98%. And crush all the above raw materials to the powder that can pass through a 60 mesh sieve;
[0013] 2. prepare drug core o...
Embodiment 2
[0021] Manufactured by:
[0022] 1. Raw materials for preparing the drug core: rutile, wollastonite, silicon-manganese alloy, iron powder, nickel powder, cryolite, feldspar, ferro-titanium, ferro-boron, medium-carbon ferromanganese, magnesia, quartz and fluorite. Requirements TiO in rutile 2 The content is 96%; CaSiO in wollastonite 3 The content of Ni in silicon-manganese alloy is 67%; Si22% in silicon-manganese alloy, Mn78%; Fe content in iron powder is 98%; Ni content in nickel powder is 99%; Na in cryolite 3 AlF 6 The content is 98%; SiO in feldspar 2 68%, Al 2 o 3 18%; Ti21% in ferro-titanium; B21% in ferroboron; Mn80% in medium carbon ferromanganese; MgO content in magnesia is 98%; SiO in quartz 2 The content is 98%; CaF in fluorite 2 The content is 98%. And crush all the above raw materials to the powder that can pass through a 60 mesh sieve;
[0023] 2. prepare drug core of the present invention by the weight percentage of following raw material:
[0024] 33%...
Embodiment 3
[0031] Manufactured by:
[0032] 1. Raw materials for preparing the drug core: rutile, wollastonite, silicon-manganese alloy, iron powder, nickel powder, cryolite, feldspar, ferro-titanium, ferro-boron, medium-carbon ferromanganese, magnesia, quartz and fluorite. Requirements TiO in rutile 2 The content is 96%; CaSiO in wollastonite 3 The content of Ni in silicon-manganese alloy is 67%; Si22% in silicon-manganese alloy, Mn78%; Fe content in iron powder is 98%; Ni content in nickel powder is 99%; Na in cryolite 3 AlF 6 The content is 98%; SiO in feldspar 2 68%, Al 2 o 3 18%; Ti21% in ferro-titanium; B21% in ferroboron; Mn80% in medium carbon ferromanganese; MgO content in magnesia is 98%; SiO in quartz 2 The content is 98%; CaF in fluorite 2 The content is 98%. And crush all the above raw materials to the powder that can pass through a 60 mesh sieve;
[0033] 2. prepare drug core of the present invention by the weight percentage of following raw material:
[0034] 30%...
PUM
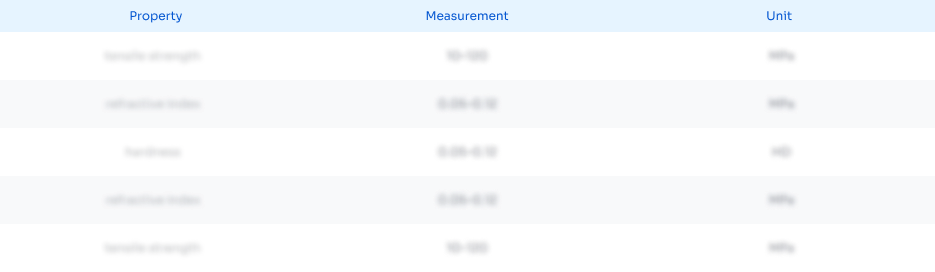
Abstract
Description
Claims
Application Information

- R&D
- Intellectual Property
- Life Sciences
- Materials
- Tech Scout
- Unparalleled Data Quality
- Higher Quality Content
- 60% Fewer Hallucinations
Browse by: Latest US Patents, China's latest patents, Technical Efficacy Thesaurus, Application Domain, Technology Topic, Popular Technical Reports.
© 2025 PatSnap. All rights reserved.Legal|Privacy policy|Modern Slavery Act Transparency Statement|Sitemap|About US| Contact US: help@patsnap.com