Method and device for processing surface of flux-cored welding wire during drawing flux-cored welding wire
A technology of surface treatment device and flux-cored welding wire, which is applied in the direction of manufacturing tools, welding media, welding equipment, etc., can solve the problems of manpower consumption, surface corrosion, complicated process, etc., and achieve smoothness improvement, spatter reduction, arc stability enhanced effect
- Summary
- Abstract
- Description
- Claims
- Application Information
AI Technical Summary
Problems solved by technology
Method used
Image
Examples
Embodiment Construction
[0009] The surface treatment method in the flux-cored wire drawing manufacturing of the present invention includes a surface cleaning process and a surface coating process for the drawn flux-cored wire. status online. The flux-cored welding wire in the high-speed drawing state continuously passes through the cleaning device that can clean the surface of the welding wire on-line, and then enters the coating device containing the powder granular coating material inside, and uses the compression zone of the coating die to The coating material is press-coated onto the surface of the flux-cored wire.
[0010] Coating materials used in the coating process, wherein the volume of powder particles with a particle size of less than 3 μm accounts for at least 60% of the total volume. The coating material is preferably composed of sulfonates of two alkali metals, potassium and sodium, which are beneficial to arc stability, and MoS, which is beneficial to lubrication. 2 , a mixture of gr...
PUM
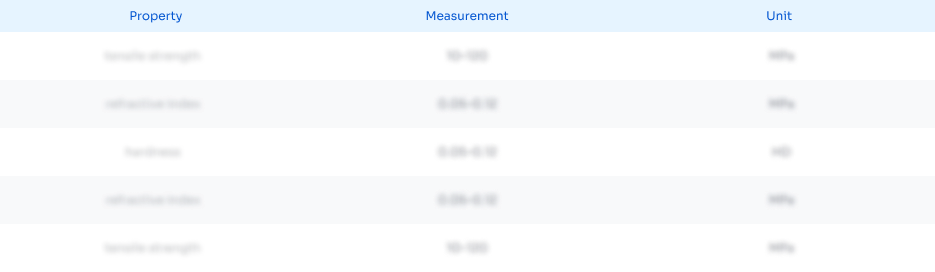
Abstract
Description
Claims
Application Information

- R&D
- Intellectual Property
- Life Sciences
- Materials
- Tech Scout
- Unparalleled Data Quality
- Higher Quality Content
- 60% Fewer Hallucinations
Browse by: Latest US Patents, China's latest patents, Technical Efficacy Thesaurus, Application Domain, Technology Topic, Popular Technical Reports.
© 2025 PatSnap. All rights reserved.Legal|Privacy policy|Modern Slavery Act Transparency Statement|Sitemap|About US| Contact US: help@patsnap.com