Constant current anode oxidation treatment method for surfaces of aluminum and aluminum alloy materials
An aluminum alloy material and anodizing technology, which is applied to the surface of aluminum and aluminum alloy materials under constant current conditions, anodizing treatment, and the field of surface treatment of aluminum and aluminum alloy materials. problem, to achieve the effect of small loss, excellent decoration and high hardness
- Summary
- Abstract
- Description
- Claims
- Application Information
AI Technical Summary
Problems solved by technology
Method used
Image
Examples
Embodiment 1
[0025] 1: Pretreatment of raw materials
[0026] Choose ordinary aluminum pots as raw materials, and then pre-treat the surface. The purpose of pre-treatment is to remove or modify the dirt and defects on the surface of aluminum pots, such as dust, metal oxides, residual oil, and asphalt marks. , Finger prints, welding flux and corrosive salts, metal burrs, slight scratches, etc. Therefore, before the oxidation treatment, chemical and physical methods are used to clean the surface of the product necessary to expose the pure metal substrate, so as to facilitate the smooth progress of anodic oxidation and coloring.
[0027] The main process of pre-processing is as follows:
[0028] (1) Degreasing: Degrease the above-mentioned common aluminum pot with NaOH solution with a concentration of 50-200g / L at a temperature of 40-80°C for 0.5-3min, wash with water after degreasing, and use 100-500g / L NaOH solution after washing. L nitric acid solution to neutralize and remove ash, degre...
Embodiment 2
[0037] The raw materials and their pretreatment process are the same as those in Example 1, and will not be repeated here.
[0038] Two: Determination of the composition of the composite electrolyte:
[0039] According to the requirements for gray-white oxide film layer on aluminum cookware.
[0040] Boric acid: 20g / L, sodium hypophosphite 10g / L, sulfosalicylic acid 6g / L.
[0041] When preparing a composite electrolyte, first dissolve all the above components with deionized water to make a concentrated solution, and then prepare a composite hydrolyzate in an oxidation tank as needed. Since the composite hydrolyzate will volatilize due to heating up during the anodic oxidation process, To be replenished in time.
[0042] Three: constant current anodizing treatment on the surface of aluminum pots and utensils:
[0043] An aluminum pan is used as an anode and placed in the composite electrolyte solution, wherein the temperature of the composite electrolyte solution is controll...
Embodiment 3
[0045] The raw materials and their pretreatment process are the same as those in Example 1, and will not be repeated here.
[0046] Two: Determination of the composition of the composite electrolyte:
[0047] According to the requirements for gray-white oxide film layer on aluminum cookware.
[0048] Boric acid: 40g / L, sodium hypophosphite 8g / L, sulfosalicylic acid 5g / L.
[0049] When preparing a composite electrolyte, first dissolve all the above components with deionized water to make a concentrated solution, and then prepare a composite hydrolyzate in an oxidation tank as needed. Since the composite hydrolyzate will volatilize due to heating up during the anodic oxidation process, To be replenished in time.
[0050] Three: constant current anodizing treatment on the surface of aluminum pots and utensils:
[0051] An aluminum pan is used as an anode and placed in the composite electrolyte solution, wherein the temperature of the composite electrolyte solution is controlle...
PUM
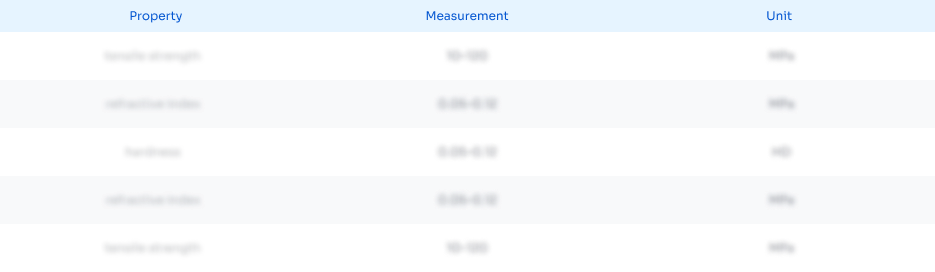
Abstract
Description
Claims
Application Information

- R&D
- Intellectual Property
- Life Sciences
- Materials
- Tech Scout
- Unparalleled Data Quality
- Higher Quality Content
- 60% Fewer Hallucinations
Browse by: Latest US Patents, China's latest patents, Technical Efficacy Thesaurus, Application Domain, Technology Topic, Popular Technical Reports.
© 2025 PatSnap. All rights reserved.Legal|Privacy policy|Modern Slavery Act Transparency Statement|Sitemap|About US| Contact US: help@patsnap.com