Reinforced textile type glass fiber treating compound and preparation thereof
A sizing and textile-type technology, which is applied in the field of reinforced textile glass fiber sizing and its preparation, can solve the problems of material waste and complicated process, and achieve the effect of no washing process, simple preparation and use process, and good clustering
- Summary
- Abstract
- Description
- Claims
- Application Information
AI Technical Summary
Problems solved by technology
Method used
Examples
Embodiment 1
[0047] The preparation method of reinforced textile glass fiber sizing agent:
[0048] A. Hydrolysis of silane coupling agent:
[0049] Add acetic acid to 500 grams of deionized water to adjust the pH value to 3-4, stir slowly at 300 rpm, add 3 grams of silane coupling agent, and continue stirring for 30-50 minutes. The stirring can be stopped when the solution is clear and free of oil droplets. And control the pH value to be less than 6 to make coupling agent hydrolyzate;
[0050] B. Dissolution preparation of solid antistatic agent:
[0051] After heating 100 grams of deionized water to 80°C, add 1 gram of solid antistatic agent, stir slowly until it is completely dissolved, and then cool to room temperature to prepare an antistatic agent solution;
[0052] C. Add the above-mentioned coupling agent hydrolyzate and antistatic agent solution into the configuration kettle, add 0.5 grams of lubricant, 80 grams of polyvinyl acetate emulsion, 20 grams of polyester emulsion, 50 g...
Embodiment 2
[0054] A. Hydrolysis of silane coupling agent:
[0055] Add acetic acid to 500 grams of deionized water to adjust the pH value to 3 to 4, stir slowly at 300 rpm, add 4 grams of silane coupling agent, and continue stirring for 30 to 50 minutes. The stirring can be stopped when the solution is clear and free of oil droplets. , and control the pH value to be less than 6 to make a coupling agent hydrolyzate;
[0056] B. Dissolution preparation of solid antistatic agent:
[0057] After heating 100 grams of deionized water to 80°C, add 2 grams of solid antistatic agent, stir slowly, and cool to room temperature until it is completely dissolved;
[0058]C. Add the coupling agent hydrolyzate and antistatic agent solution prepared above into the configuration kettle, add 0.4 grams of lubricant, 60 grams of polyvinyl acetate emulsion, 40 grams of polyester emulsion, and 40 grams of epoxy resin emulsion , 6 grams of polyurethane emulsion, 4 grams of surfactant and the remaining part of...
PUM
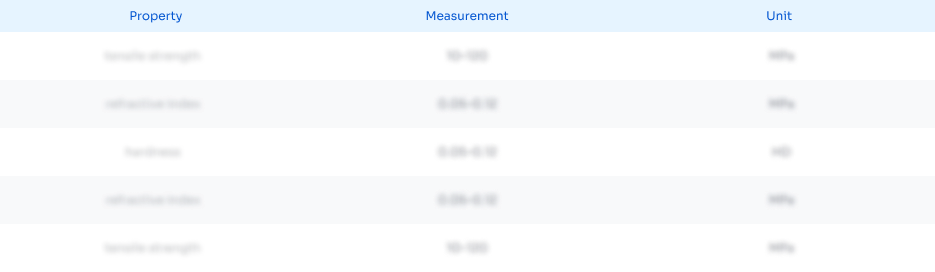
Abstract
Description
Claims
Application Information

- R&D
- Intellectual Property
- Life Sciences
- Materials
- Tech Scout
- Unparalleled Data Quality
- Higher Quality Content
- 60% Fewer Hallucinations
Browse by: Latest US Patents, China's latest patents, Technical Efficacy Thesaurus, Application Domain, Technology Topic, Popular Technical Reports.
© 2025 PatSnap. All rights reserved.Legal|Privacy policy|Modern Slavery Act Transparency Statement|Sitemap|About US| Contact US: help@patsnap.com