Hot dip galvanizing annealing process and high temperature annealing furnace
An annealing process and an annealing furnace technology, applied in the field of metallurgy, can solve the problems of cumbersome equipment, large production and maintenance, and large secondary investment in equipment, etc., and achieve the effect of reducing primary investment cost, reducing equipment investment, and energy-saving equipment investment
- Summary
- Abstract
- Description
- Claims
- Application Information
AI Technical Summary
Problems solved by technology
Method used
Image
Examples
Embodiment Construction
[0025] Below in conjunction with accompanying drawing 3,4 and 5 the specific embodiment of the present invention is described further:
[0026] 1) The high-temperature annealing furnace includes a non-oxidizing regenerative heating furnace 10 , a non-heating holding furnace 8 and a rapid cooling section 9 .
[0027] Non-oxidation regenerative heating furnace 10: the heating furnace is provided with external combustion chambers 4a and 4b arranged in pairs, which are independent of the furnace hearth, and are arranged in pairs on both sides of the furnace hearth 6 respectively. The reversing valve 7 is externally connected to the devices 3a and 3b, and is controlled by the reversing valve 7, and turns into a heating combustion chamber and a heat storage combustion chamber; In the oxidative combustion mode, the combustion products enter the furnace in an incomplete combustion state after leaving the heating combustion chamber to heat the strip steel. The regenerators of the heat...
PUM
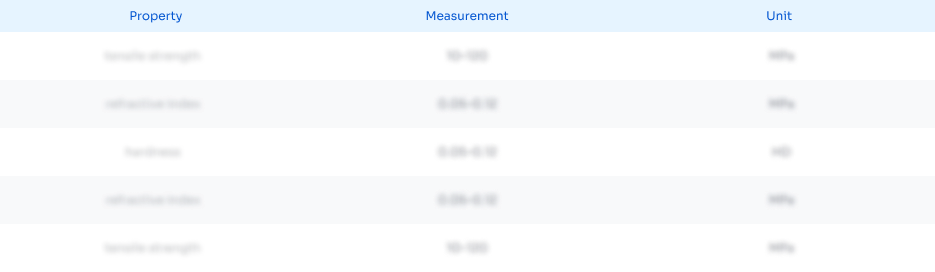
Abstract
Description
Claims
Application Information

- R&D
- Intellectual Property
- Life Sciences
- Materials
- Tech Scout
- Unparalleled Data Quality
- Higher Quality Content
- 60% Fewer Hallucinations
Browse by: Latest US Patents, China's latest patents, Technical Efficacy Thesaurus, Application Domain, Technology Topic, Popular Technical Reports.
© 2025 PatSnap. All rights reserved.Legal|Privacy policy|Modern Slavery Act Transparency Statement|Sitemap|About US| Contact US: help@patsnap.com