Coating liquid for undercoating layer formation in electrophotographic photoreceptor, and process for producing the same
A technology of electrophotography and manufacturing method, applied in optics, electrical recording, instruments, etc., can solve problems such as insufficient performance, and achieve the effects of high charging potential and sensitivity, uniform film thickness, and excellent electrical characteristics
- Summary
- Abstract
- Description
- Claims
- Application Information
AI Technical Summary
Problems solved by technology
Method used
Image
Examples
Embodiment 1
[0341] The rutile titanium dioxide ("TTO55N" manufactured by Ishihara Sangyo Co., Ltd.) with an average primary particle diameter of 40 nm and methyldimethoxysilane ("TSL8117" manufactured by Toshiba Silicone Co., Ltd.) weighing 3% by weight of the titanium dioxide were used Scheer mixer mixed to obtain surface-treated titanium dioxide, 90 parts of the obtained surface-treated titanium dioxide, 30 parts of methanol (hereinafter sometimes referred to as "MeOH"), 60 parts of tetrahydrofuran (hereinafter sometimes referred to as "THF ") mixed to form a raw material slurry, using zirconia beads (YTZ manufactured by NIKKATO Co., Ltd.) with an average particle diameter of about 100 μm as a dispersion medium, and using a mill volume of about 0.15L ULTRAAPEX MILL manufactured by Kotobukiya Co., Ltd. (UAM- Model 015), 1 kg of the raw material slurry was subjected to a dispersion treatment for 1 hour under a liquid circulation state with a rotor circumferential speed of 10 m / sec and a liqui...
Embodiment 2
[0352] As a dispersion medium when dispersing by ULTRA APEX MILL, zirconia beads (manufactured by NIKKATO, YTZ) with an average particle diameter of about 50 μm were used. Except for this, the same procedure as in Example 1 was carried out to produce the "undercoat layer forming coating"液SE2". In SE2, the cumulative 90% particle size of the metal oxide particles is 0.12 μm.
Embodiment 3
[0354]A mixture of 30 parts of melamine resin, 80 parts of n-butanol, 36 parts of paraformaldehyde, and 0.03 parts of 1N hydrochloric acid aqueous solution was reacted for 2 hours under reflux dehydration at a temperature of 100°C. The n-butanol was distilled off to obtain a solid content of 50 weight. % Of resin liquid. The "titanium dioxide dispersion TB1" was mixed with the resin solution and 0.25 parts of dinonylnaphthalenedisulfonic acid to dissolve it, and then filtered with a PTFE membrane filter (manufactured by ADVANTEC Corporation, Mitex LC) with a pore size of 5 μm to prepare the following final Composition "Coating Solution SE3 for Undercoat Layer Formation". In SE3, the cumulative 90% particle size of the metal oxide particles is 0.13 μm.
[0355] Curable binder resin 30 parts
[0356] 90 parts of surface-treated titanium dioxide
[0357] MeOH 30 parts
[0358] 60 parts of THF
[0359] BuOH 30 parts
[0360] Solid content concentration 50%
PUM
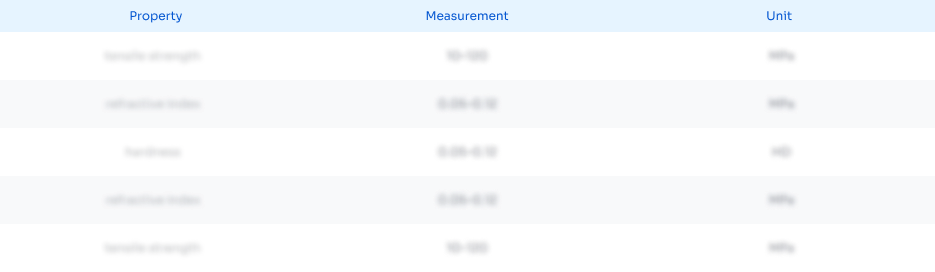
Abstract
Description
Claims
Application Information

- R&D Engineer
- R&D Manager
- IP Professional
- Industry Leading Data Capabilities
- Powerful AI technology
- Patent DNA Extraction
Browse by: Latest US Patents, China's latest patents, Technical Efficacy Thesaurus, Application Domain, Technology Topic, Popular Technical Reports.
© 2024 PatSnap. All rights reserved.Legal|Privacy policy|Modern Slavery Act Transparency Statement|Sitemap|About US| Contact US: help@patsnap.com