Production method for solid castoff composite multi-story building template
A solid waste, multi-storey building technology, applied in the on-site preparation of building components, solid waste management, construction and other directions, can solve the complex treatment of fiber length and moisture content, does not involve the use of fly ash, and cannot guarantee wood plastic Product size setting and other issues, to achieve the effect of good surface finish
- Summary
- Abstract
- Description
- Claims
- Application Information
AI Technical Summary
Problems solved by technology
Method used
Examples
Embodiment 1
[0037] Mix 40 parts of fly ash and 1.5 parts of silane coupling agent at high speed for 10 minutes at 80°C; mix 2 parts of EVA, 1 part of anionic surfactant, 1 part of stearic acid, 2 parts of paraffin, antioxidant 1010 0.6 parts, 4 parts of flame retardant, 0.4 parts of phosphite triester, 3 parts of carbon black, mixed with 100 parts of granulated waste plastic PE; mixed at 85°C for 10 minutes at high speed, and then mixed this material with the treated Fly ash is mixed and extruded through an extruder (head temperature is 190°C). Extrude 60 parts of wood flour, 40 parts of granulated waste plastic PE, 1.5 parts of acrylate, 1.5 parts of dioctyl phthalate, 1 part of stearic acid, 3 parts of paraffin, and 0.8 parts of pentachlorophenol Machine extrusion (head temperature: 190°C) to make wood-plastic mixture. Then put half of the extruded plastic ash mixture on the bottom layer of the mold, put the wood-plastic mixture on it, and put the other half of the plastic ash mixture ...
Embodiment 2
[0039] Mix 50 parts of fly ash and 2 parts of silane coupling agent at high speed for 10 minutes at 90°C; mix 100 parts of waste plastic PS after granulation with 2 parts of anionic surfactant, 1.5 parts of stearic acid, carbon black 2 parts, 4 parts of paraffin, 0.2 parts of antioxidant 1010, 3 parts of EVA, 3 parts of flame retardant, 0.1 part of triphosphite, add together, mix at 80 °C for 10 minutes at high speed, and then mix with the surface-treated The fly ash is mixed and extruded through an extruder (head temperature is 160°C). Extrude 40 parts of sawdust, 60 parts of granulated waste plastic PS, 2 parts of acrylate, 2 parts of dioctyl phthalate, 3 parts of stearic acid, 4 parts of paraffin, and 0.6 part of pentachlorophenol Machine extrusion (head temperature is 160°C), then put the wood-plastic mixture into a mold at 110°C, put half of the plastic-ash mixture on the bottom layer, put the wood-plastic mixture on it, and put the other half of the plastic on the top la...
Embodiment 3
[0040] Mix 30 parts of fly ash and 0.8 parts of silane coupling agent at high speed for 10 minutes at 70°C; mix 100 parts of granulated waste plastic PP with 0.5 parts of anionic surfactant, 1 part of stearic acid, and 3 parts of paraffin parts, 0.4 parts of antioxidant 1010, 1 part of EVA, 5 parts of carbon black, 0.3 parts of phosphite triester, 6 parts of flame retardant, mixed together at 100°C for 10 minutes at high speed; The fly ash is mixed and extruded through an extruder (head temperature is 200°C). 50 parts of sawdust, 50 parts of granulated waste plastic PP, 1.5 parts of acrylate, 0.5 part of dioctyl phthalate, 2 parts of stearic acid, 5 parts of paraffin, and 0.5 part of pentachlorophenol are passed through the extruder Extrude (head temperature is 200°C) to make wood-plastic mixture. Then put half of the extruded plastic ash mixture on the bottom layer of the mold, put the wood-plastic mixture on it, and put the other half of the plastic ash mixture on the upper...
PUM
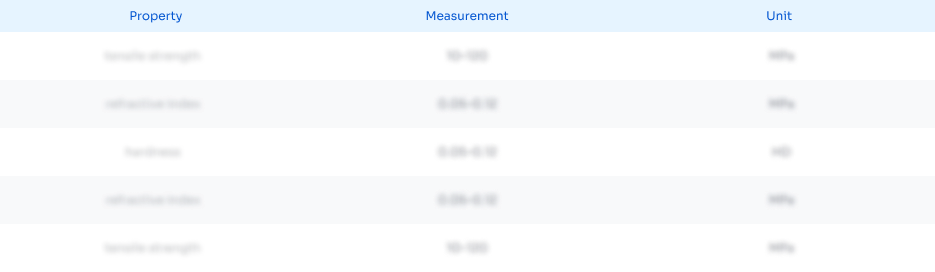
Abstract
Description
Claims
Application Information

- R&D
- Intellectual Property
- Life Sciences
- Materials
- Tech Scout
- Unparalleled Data Quality
- Higher Quality Content
- 60% Fewer Hallucinations
Browse by: Latest US Patents, China's latest patents, Technical Efficacy Thesaurus, Application Domain, Technology Topic, Popular Technical Reports.
© 2025 PatSnap. All rights reserved.Legal|Privacy policy|Modern Slavery Act Transparency Statement|Sitemap|About US| Contact US: help@patsnap.com