Method for manufacturing foil by composite oxidation film at low pressure
A composite oxide film and manufacturing method technology, which is applied in anodic oxidation, electrolytic capacitors, electrical components, etc., can solve the problems of oxide film thickness, low processing efficiency, electrostatic capacity and hydration resistance, and improve hydration resistance performance effect
- Summary
- Abstract
- Description
- Claims
- Application Information
AI Technical Summary
Problems solved by technology
Method used
Image
Examples
Embodiment 1
[0035] A method for manufacturing composite oxide film into foil at low pressure, comprising the following steps:
[0036] According to the method of the present invention, the formation foil with the highest formation voltage of 20V is made, and the specific method is as follows:
[0037] a. The low-pressure corrosion foil is chemically treated in 0.4mol / L ammonium adipate solution at 70°C, divided into four stages, and the voltages are: the first stage voltage of the four-stage chemical formation is: 20v×35% =7v; the second voltage of the four-level formation is: 20×60%=12v; the third-level voltage of the four-level formation is: 20×80%=16v; the fourth-level voltage of the four-level formation is: 20×100 %=20v means the highest conversion voltage is 20V;
[0038] b. Soak the formed foil that has been chemically treated in step a in 0.01mol / L sodium silicate solution at 60°C for 2 minutes, and then wash it with pure water;
[0039] c. Place the formed foil after step b at 7...
Embodiment 2
[0054] A method for manufacturing composite oxide film into foil at low pressure, comprising the following steps:
[0055] According to the method of the present invention, the formation foil with the highest formation voltage of 100V is made, and the specific method is as follows:
[0056] a. The low-pressure corrosion foil is chemically treated in 0.6mol / L ammonium adipate solution at 85°C, divided into four stages, and the voltages are: the first stage voltage of the four-stage chemical formation is: 100v×35% =35v; the second voltage of the four-level formation is: 100×60%=60v; the third-level voltage of the four-level formation is: 100×80%=80v; the fourth-level voltage of the four-level formation is: 100×100 %=100v means the highest conversion voltage is 100V;
[0057] b. Soak the formed foil that has been chemically treated in step a in 0.01mol / L sodium silicate solution at 60°C for 6 minutes, and then wash it with pure water;
[0058] c. Place the formed foil after ste...
Embodiment 3
[0073] A method for manufacturing composite oxide film into foil at low pressure, comprising the following steps:
[0074] According to the method of the present invention, the formation foil with the highest formation voltage of 50V is made, and the specific method is as follows:
[0075] a. The low-pressure corrosion foil is subjected to chemical conversion treatment in 0.9mol / L ammonium adipate solution at 80°C, divided into three stages, and the voltages are: the first stage voltage of the three-stage chemical formation is: 50v×40% =20v; the second level voltage of the three-level formation is: 50×80%=40v; the third-level voltage of the three-level formation is: 50×100%=50v; that is, the highest formation voltage is 50V;
[0076] b. Soak the formed foil that has been chemically treated in step a in 0.01mol / L sodium silicate solution at 60°C for 6 minutes, and then wash it with pure water;
[0077] c. Place the formed foil after step b at 80°C in a 0.9 mol / L ammonium adipa...
PUM
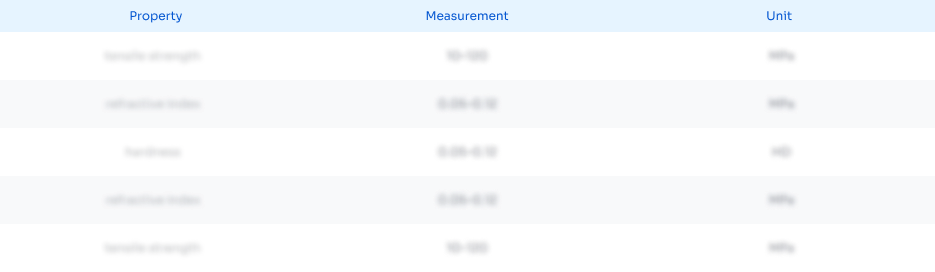
Abstract
Description
Claims
Application Information

- R&D
- Intellectual Property
- Life Sciences
- Materials
- Tech Scout
- Unparalleled Data Quality
- Higher Quality Content
- 60% Fewer Hallucinations
Browse by: Latest US Patents, China's latest patents, Technical Efficacy Thesaurus, Application Domain, Technology Topic, Popular Technical Reports.
© 2025 PatSnap. All rights reserved.Legal|Privacy policy|Modern Slavery Act Transparency Statement|Sitemap|About US| Contact US: help@patsnap.com