Method for purifying non-metal inclusion in magnesium alloy by ultrasonic agglomeration
A technology of non-metallic inclusions and magnesium alloys, applied in the field of material science, can solve the problems of insufficient and clear understanding, no industrial application, and low production efficiency
- Summary
- Abstract
- Description
- Claims
- Application Information
AI Technical Summary
Problems solved by technology
Method used
Image
Examples
Embodiment 1
[0044] Metal magnesium and other alloying elements are melted in the iron crucible of the resistance heating furnace, and CO is introduced under the condition of 50-100°C above the liquidus line 2 / SF 6 Gas, the flow rate is 5 ~ 10ml / min, the gas composition is CO by volume ratio 2 : SF 6 =100:1, carry out mechanical stirring, the stirring speed is 30~60rpm, and the stirring time is 10~15min. After the stirring is finished, adopt semi-continuous casting equipment to carry out semi-continuous casting to obtain magnesium alloy billets; 200mm parts are removed from the tail ends, and the remaining middle part is used as a purified magnesium alloy cast slab, and the magnesium alloy is GW103K (Mg-10Gd-3Y-0.6Zr) magnesium alloy.
[0045] Place the magnesium alloy billet in a preheated crucible with a lid at 200°C; 2 / SF 6 gas and heated with stirring, CO 2 / SF 6 The gas flow rate is 5 ~ 10ml / min, CO 2 / SF 6 Gas composition by volume ratio is CO 2 : SF 6 =100:1, the stirrin...
Embodiment 2
[0050] The preparation method of the magnesium alloy slab is the same as that in Example 1, and the magnesium alloy is a GW103K magnesium alloy.
[0051] Place the magnesium alloy billet in a preheated crucible with a lid at 300°C; 2 / SF 6 gas and heated with stirring, CO 2 / SF 6 The gas flow rate is 5 ~ 10ml / min, CO 2 / SF 6 Gas composition by volume ratio is CO 2 : SF 6 =100:1, the stirring speed is 30-60rpm, and heated to 710°C, so that the magnesium alloy billet becomes a magnesium alloy melt.
[0052] The ultrasonic rod with the ultrasonic generator is preheated to 710°C, inserted into the magnesium alloy melt, and then ultrasonic waves are applied to the magnesium alloy. The ultrasonic frequency is 20kHz, and the ultrasonic sound intensity is 0.77W / cm 2 (total power 30W), 0.9W / cm 2 (total power 35W) and 2.7W / cm 2 (total power 105W), the time is 50s; after the ultrasonic wave is applied, remove the ultrasonic rod, let the magnesium alloy melt stand for 30s, and th...
Embodiment 3
[0055] The preparation method of the magnesium alloy slab is the same as that in Example 1, and the magnesium alloy is a GW103K magnesium alloy.
[0056] Place the magnesium alloy billet in a preheated crucible with a lid, the preheating temperature is 400°C; 2 / SF 6 Mix gas and heat and stir, CO 2 / SF 6 The gas flow rate is 5 ~ 10ml / min, CO 2 / SF 6 Gas composition by volume ratio is CO 2 : SF 6 =100:1, the stirring speed is 30-60rpm, and heated to 745°C, so that the magnesium alloy billet becomes a magnesium alloy melt.
[0057] The ultrasonic rod using the ultrasonic generator is preheated to 745°C, inserted into the magnesium alloy melt, and then applies ultrasonic waves to the magnesium alloy. The ultrasonic frequency is 20kHz, and the ultrasonic sound intensity is 0.9W / cm respectively. 2 (total power 35W), 2.96W / cm 2 (total power 115W), 7.26W / cm 2 (total power 280W) and 20.96W / m 2 (total power 815W), the time is 50s; after the ultrasonic wave is applied, the ult...
PUM
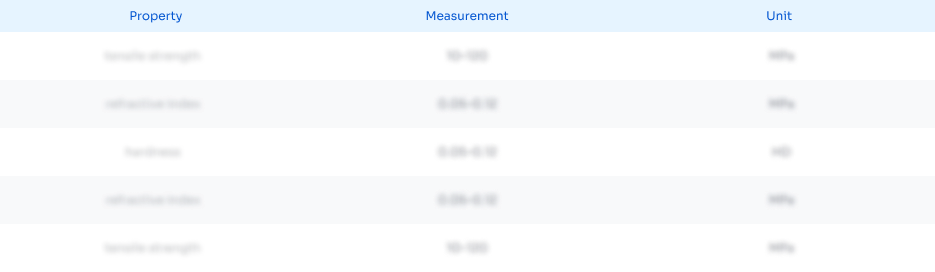
Abstract
Description
Claims
Application Information

- R&D Engineer
- R&D Manager
- IP Professional
- Industry Leading Data Capabilities
- Powerful AI technology
- Patent DNA Extraction
Browse by: Latest US Patents, China's latest patents, Technical Efficacy Thesaurus, Application Domain, Technology Topic, Popular Technical Reports.
© 2024 PatSnap. All rights reserved.Legal|Privacy policy|Modern Slavery Act Transparency Statement|Sitemap|About US| Contact US: help@patsnap.com