Corroson-resistant steel material for crude oil storage tank, and crude oil storage tank
A crude oil tank and steel technology, which is applied in the field of crude oil tanks and corrosion-resistant steel, can solve the problems of large construction and inspection costs, coating film damage and corrosion, and achieve excellent general corrosion resistance and local corrosion resistance.
- Summary
- Abstract
- Description
- Claims
- Application Information
AI Technical Summary
Problems solved by technology
Method used
Image
Examples
Embodiment 1
[0088] Steels having various compositions of Nos. 1 to 33 shown in Table 1 are melted in a vacuum melting furnace or a converter, and these steel slabs are reheated to 1200°C, and hot-rolled at 800°C as the final rolling finish temperature , to make a thick steel plate with a thickness of 16mm.
[0089] From the steel plates No.1 to 33 obtained in this way, cut out a square piece with a width of 50 mm x a length of 50 mm x a thickness of 15 mm. ~10μm, 15~25μm, 50~70μm four kinds of inorganic zinc primer thickness, make the test piece. Then, while covering the end surface and inner surface of the test piece with anticorrosive paint, only on the upper surface of the test surface is uniformly coated with oil sludge containing crude oil components taken from the actual oil tank to form a corrosion resistance test piece. test piece. Here, two types of corrosion test pieces having different surface states were produced. That is, a test piece (test 1) in which oil sludge was unifo...
Embodiment 2
[0104] From the same No.1~33 steel plates that are used in Example 1, cut out the rectangular small piece of wide 25mm * length 48mm * thick 4mm, after its surface is carried out sandblasting, coating film thickness is 0 μ m ( No coating), 5 ~ 10μm, 15 ~ 25μm, 50 ~ 70μm four kinds of inorganic zinc primers, made of test pieces, and then, in order to accelerate the corrosion resistance test, on the surface of the above coating film, formed to reach the steel The X-shaped cuts on the surface were used to make the damage area ratio 1.0%, and a corrosion test piece was made.
[0105] For these test pieces, use figure 2 The corrosion test apparatus shown in the figure is a general corrosion test that is likely to occur in the environment inside the upper deck of a crude oil tank. The corrosion test device is composed of a corrosion test tank 9 and a temperature control plate 10, and water 13 is injected into the corrosion test tank 9, and the temperature is maintained at 40°C. I...
PUM
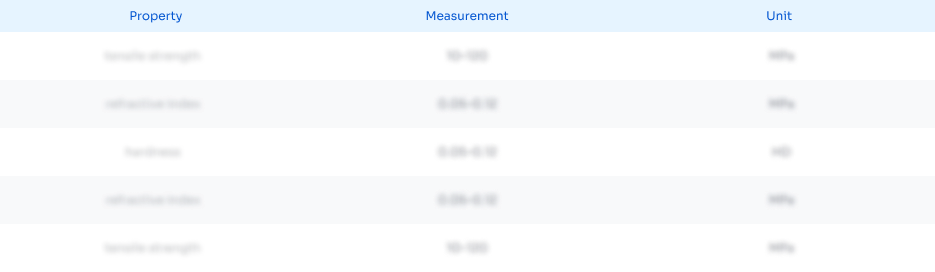
Abstract
Description
Claims
Application Information

- R&D Engineer
- R&D Manager
- IP Professional
- Industry Leading Data Capabilities
- Powerful AI technology
- Patent DNA Extraction
Browse by: Latest US Patents, China's latest patents, Technical Efficacy Thesaurus, Application Domain, Technology Topic, Popular Technical Reports.
© 2024 PatSnap. All rights reserved.Legal|Privacy policy|Modern Slavery Act Transparency Statement|Sitemap|About US| Contact US: help@patsnap.com