Precision vibration damping assembly and vibration damping platform composed of the assembly
A vibration damping component and sophisticated technology, applied in springs/shock absorbers, vibration suppression adjustment, microlithography exposure equipment, etc., can solve problems such as increasing the inertia of the worktable, complicating the structure of the moving table, and increasing the difficulty of control. , to achieve the effect of achieving stiffness, improving vibration isolation effect, and high attenuation rate
- Summary
- Abstract
- Description
- Claims
- Application Information
AI Technical Summary
Problems solved by technology
Method used
Image
Examples
Embodiment Construction
[0023] The structure and working principle of the present invention are further described below in conjunction with design examples and accompanying drawings.
[0024] Such as figure 1 As shown, the precision damping assembly provided by the present invention is composed of an outer frame, a passive damping component and an active damping actuator.
[0025] The frame 1 is hollow cylindrical, and the side wall of the frame 1 is provided with an air inlet 2, and a plurality of exhaust channels 4 are respectively arranged under the side wall of the frame 1 to release the pressure gas flowing out of the cylindrical air bearing, An air inlet 10 for connecting an external air source is opened at the bottom thereof. The piston rod 6 is cylindrical with an H-shaped section and is located in the cylindrical cavity of the frame 1 .
[0026] When the independent air source supplies air through the air inlet 10, the pressure gas flows out from the air inlet 2 on the frame 1, forming a l...
PUM
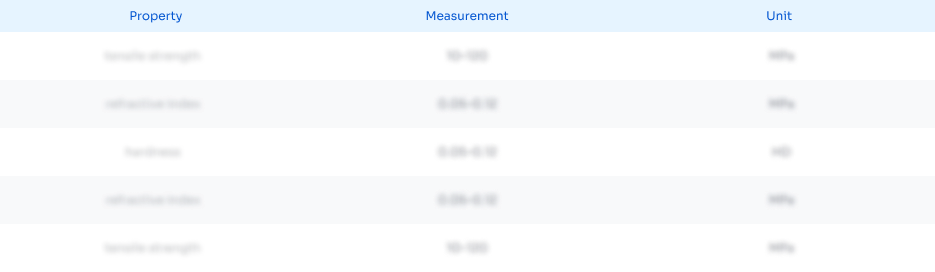
Abstract
Description
Claims
Application Information

- R&D
- Intellectual Property
- Life Sciences
- Materials
- Tech Scout
- Unparalleled Data Quality
- Higher Quality Content
- 60% Fewer Hallucinations
Browse by: Latest US Patents, China's latest patents, Technical Efficacy Thesaurus, Application Domain, Technology Topic, Popular Technical Reports.
© 2025 PatSnap. All rights reserved.Legal|Privacy policy|Modern Slavery Act Transparency Statement|Sitemap|About US| Contact US: help@patsnap.com