Method for extracting molybdenum by roasting high impurity sodium carbonate nickel-ferro-molybdenum
A ferroalloy and sodium carbonate technology, applied in the direction of improving process efficiency, can solve the problems of large consumption of sodium carbonate reagent, loss of Mo, V, and high production cost, and achieve good roasting effect, low production cost and fast reaction speed. Effect
- Summary
- Abstract
- Description
- Claims
- Application Information
AI Technical Summary
Problems solved by technology
Method used
Image
Examples
Embodiment 1
[0026] Add 35g Na to 100g high-impurity nickel-molybdenum-iron alloy powder 2 CO 3 (1.6 times the stoichiometric sum of the roasting reactions of Mo and V) and 25g CaO (1.1 times the stoichiometric sum of the roasting reactions of P, As and Si) were mixed and ground to -150 mesh, and roasted at 550°C for 4 hours. Liquid ratio 1:4, add water and stir, then add Na2CO 3 Adjust the pH of the solution to 11, stir and leach for 2 hours at 80°C, and then filter. The experimental result (%) of high impurity nickel-molybdenum-iron alloy sodium carbonate roasting is as follows:
[0027] Mo P As Si V Ni Fe molybdenum ferroalloy 18.23 5.48 0.301 4.03 1.52 8.17 51.23 Leach residue 0.281 3.89 0.214 2.87 0.311 5.83 36.58 Leaching rate 97.84 --- --- --- 71.36 --- ---
Embodiment 2
[0029] Add 28g Na to 100g high-impurity nickel-molybdenum-iron alloy powder 2 CO 3 , 15g CaO and 10g Ca(OH) 2 Mix and grind to -150 mesh, roast at 650°C for 3 hours, add water to the calcined sand at a solid-to-liquid ratio of 1:3 and stir, then add NaOH to adjust the pH of the solution to 12, stir and leach at 70°C for 2.5 hours, and then filter. The experimental result (%) of high impurity nickel-molybdenum-iron alloy sodium carbonate roasting is as follows:
[0030] Mo P As Si V Ni Fe molybdenum ferroalloy 18.23 5.48 0.301 4.03 1.52 8.17 51.23 Leach residue 0.265 3.81 0.210 2.85 0.245 5.82 36.60 Leaching rate 97.96 --- --- --- 77.43 --- ---
Embodiment 3
[0032] Add 25g Na to 100g high-impurity nickel-molybdenum-iron alloy 2 CO 3 and 30g Ca(OH) 2 Mix and grind to -180 mesh, roast at 700°C for 2 hours, add water and stir the calcined sand at a solid-to-liquid ratio of 1:2, add lime milk to adjust the pH of the solution to 13, stir and leach at 60°C for 4 hours, and then filter. The experimental result (%) of high impurity nickel-molybdenum-iron alloy sodium carbonate roasting is as follows:
[0033] Mo P As Si V Ni Fe molybdenum ferroalloy 16.25 7.41 1.27 2.24 1.41 10.03 53.78 Leach residue 0.236 5.44 0.932 1.65 0.173 7.38 39.53 Leaching rate 98.02 --- --- --- 82.81 --- ---
PUM
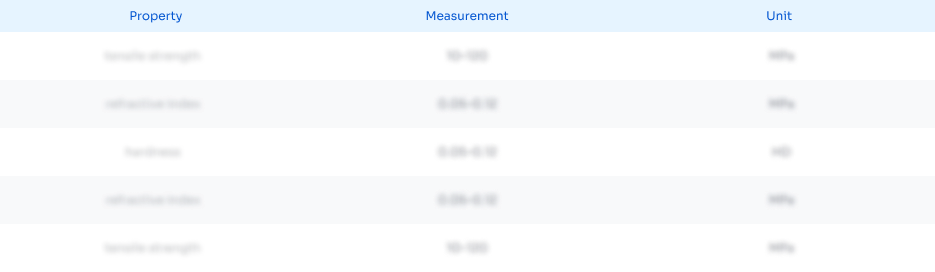
Abstract
Description
Claims
Application Information

- R&D
- Intellectual Property
- Life Sciences
- Materials
- Tech Scout
- Unparalleled Data Quality
- Higher Quality Content
- 60% Fewer Hallucinations
Browse by: Latest US Patents, China's latest patents, Technical Efficacy Thesaurus, Application Domain, Technology Topic, Popular Technical Reports.
© 2025 PatSnap. All rights reserved.Legal|Privacy policy|Modern Slavery Act Transparency Statement|Sitemap|About US| Contact US: help@patsnap.com