Cemented carbide/steel composite roller and preparation method thereof
A cemented carbide and composite roll technology, applied in metal rolling, metal rolling, rolls, etc., can solve the problems of low-temperature environment operation with low torque resistance and shear force, complex preparation process of composite rolls, etc., and achieve good oxidation resistance. , Enhance the anti-oxidation performance, the effect of reducing residual stress
- Summary
- Abstract
- Description
- Claims
- Application Information
AI Technical Summary
Problems solved by technology
Method used
Image
Examples
specific Embodiment approach 1
[0010] Embodiment 1: In this embodiment, the cemented carbide / steel composite roll is made of a cemented carbide outer ring, a steel inner ring and pre-set brazing material.
[0011] The cemented carbide outer ring in this embodiment is made by powder metallurgy technology; because the surface layer of the cemented carbide outer ring contains more free carbon, which affects the wettability of the solder, grinding should be used to remove Free state carbon in the surface layer.
specific Embodiment approach 2
[0012] Embodiment 2: The difference between this embodiment and Embodiment 1 is that the preset solder is composed of solder powder and binder in a volume ratio of 2:1-5. Others are the same as in the first embodiment.
specific Embodiment approach 3
[0013] Embodiment 3: The difference between this embodiment and Embodiment 2 is that the solder powder is composed of 5%-25% Cr, 2%-10% Si and Ni in the balance by mass percentage. Others are the same as in the second embodiment.
PUM
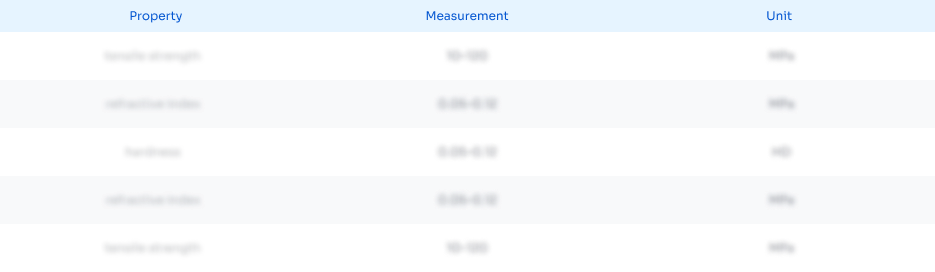
Abstract
Description
Claims
Application Information

- R&D Engineer
- R&D Manager
- IP Professional
- Industry Leading Data Capabilities
- Powerful AI technology
- Patent DNA Extraction
Browse by: Latest US Patents, China's latest patents, Technical Efficacy Thesaurus, Application Domain, Technology Topic, Popular Technical Reports.
© 2024 PatSnap. All rights reserved.Legal|Privacy policy|Modern Slavery Act Transparency Statement|Sitemap|About US| Contact US: help@patsnap.com