Smelting method for vulcanization easy cutting plastic mold steel
A technology of plastic mold steel and smelting method, which is applied in the field of smelting, can solve the problems that the steel plate flaw detection level cannot meet the requirements, the purity of molten steel cannot be guaranteed, and the inclusions cannot be removed to the maximum extent, so as to achieve performance improvement, prevention of secondary oxidation, and various item performance improvement
- Summary
- Abstract
- Description
- Claims
- Application Information
AI Technical Summary
Problems solved by technology
Method used
Examples
Embodiment 1
[0011] Example 1: The ingredients of the electric furnace are 45 tons of hot molten iron + 8 tons of pig iron + 27 tons of high-quality steel scrap + 15 tons of sponge iron. The smelting cycle of the electric furnace is 48 minutes. Tapping [C]: 0.08%, [P]: 0.007%, tapping The temperature is 1618°C, there is no oxidation slag in the ladle when the steel is tapped, the argon blowing is normal, and it is sent to the LF furnace for refining. During the refining process, the slag is deoxidized. The refining cycle is 55 minutes, and the white slag is kept for 40 minutes. The sulfur content in the molten steel is controlled to 0.003 %, slag removal to adjust the weight percentage of steel slag in molten steel to 0.8%; then send it into a vacuum furnace, feed aluminum wire into molten steel, the weight of the fed aluminum wire is 0.08% of the weight of molten steel, and then add steel slag , adjust the percentage by weight of steel slag in molten steel to be 1.5%, then keep it under th...
Embodiment 2
[0013] Example 2: The ingredients of the electric furnace are 45 tons of hot molten iron + 8 tons of pig iron + 27 tons of high-quality steel scrap + 15 tons of sponge iron. The smelting cycle of the electric furnace is 48 minutes. The temperature is 1618°C, there is no oxidation slag in the ladle when the steel is tapped, the argon blowing is normal, and it is sent to the LF furnace for refining. During the refining process, the slag is deoxidized, the refining cycle is 55 minutes, the white slag is kept for 40 minutes, and the sulfur content in the molten steel is controlled to 0.005 %, slag removal to adjust the weight percentage of steel slag in molten steel to 1%; then send it into the vacuum furnace, feed aluminum wire into the molten steel, the weight of the fed aluminum wire is 0.09% of the weight of molten steel, and then add steel slag , adjust the percentage by weight of steel slag in molten steel to be 1.7%, then keep it under a pressure of 65Pa for 20 minutes, then...
Embodiment 3
[0015] Example 3: The ingredients of the electric furnace are 45 tons of hot metal + 8 tons of pig iron + 27 tons of high-quality steel scrap + 15 tons of sponge iron. The smelting cycle of the electric furnace is 48 minutes. Tapping [C]: 0.08%, [P]: 0.007%, tapping The temperature is 1618°C, there is no oxidation slag in the ladle when the steel is tapped, the argon blowing is normal, and it is sent to the LF furnace for refining. During the refining process, the slag is deoxidized. The refining cycle is 55 minutes, and the white slag is kept for 40 minutes. %, slag removal to adjust the weight percentage of steel slag in molten steel to 1.2%; then send it into the vacuum furnace, feed aluminum wire into the molten steel, the weight of the fed aluminum wire is 0.10% of the weight of molten steel, and then add steel slag , adjust the percentage by weight of steel slag in molten steel to be 2%, then keep it under the pressure of 70Pa for 15 minutes, then release the vacuum, feed...
PUM
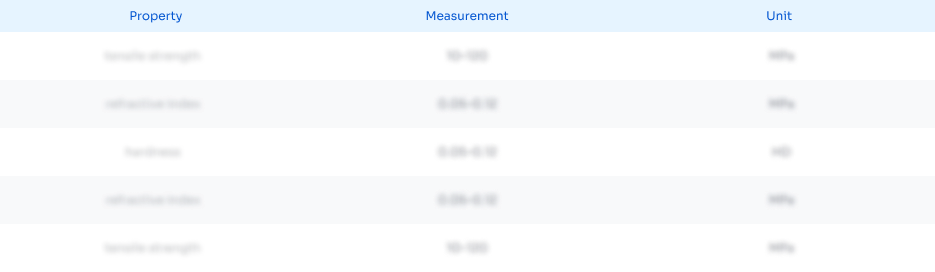
Abstract
Description
Claims
Application Information

- R&D
- Intellectual Property
- Life Sciences
- Materials
- Tech Scout
- Unparalleled Data Quality
- Higher Quality Content
- 60% Fewer Hallucinations
Browse by: Latest US Patents, China's latest patents, Technical Efficacy Thesaurus, Application Domain, Technology Topic, Popular Technical Reports.
© 2025 PatSnap. All rights reserved.Legal|Privacy policy|Modern Slavery Act Transparency Statement|Sitemap|About US| Contact US: help@patsnap.com