Method for preparing butadiene with butylene oxo-dehydrogenation of axially-located bed
An axial fixation, oxidative dehydrogenation technology, applied in chemical instruments and methods, organic chemistry, hydrocarbons, etc., can solve the problem of unsatisfactory butadiene selectivity in butene conversion, low butadiene yield, reaction It can solve the problem of high segment line speed, and achieve the effect of significant economic and social benefits, high selectivity, and steam saving.
- Summary
- Abstract
- Description
- Claims
- Application Information
AI Technical Summary
Problems solved by technology
Method used
Image
Examples
Embodiment 1
[0021] A stainless steel reactor with a reactor diameter of 3 m and a height of 4.5 m, with a catalyst bed height of 0.5 m. Butene gas phase space velocity 400h -1 The inlet temperature of the reactor is 315±2℃, the molar ratio of butene:oxygen:water in the first stage reaction is 1:0.55:16, the molar ratio of butene:oxygen in the second stage reaction is 1:0.7, and the reaction is tested for 100 hours The average data of the results are shown in Table 1.
[0022] Table 1. 100-hour test result table
[0023]
Embodiment 2
[0025] The diameter of the reactor is 3 meters, the height is 4.5 meters, and the catalyst bed height is 0.6m. Butene gas phase space velocity 400h -1 The inlet temperature of the reactor is 315±2℃, the molar ratio of butene:oxygen:water in the first stage reaction is 1:0.65:16, and the molar ratio of butene:oxygen in the second stage reaction is 1:0.65. The reaction is tested for 100 hours. The average data of the results are shown in Table 2.
[0026] Table 2. 100 hour test result table
[0027]
Embodiment 3
[0029] The two-stage reactor has a diameter of 4 meters, a height of 6 meters, and a catalyst bed height of 0.4m. The inter-stage heat exchanger uses steam to exchange heat, and the gas phase space velocity of butene in the first stage is 300h -1 , Two-stage butene gas phase space velocity 500h -1 , The molar ratio of butene:oxygen:water in the first stage reaction is 1:0.6:16, and the molar ratio of butene:oxygen in the second stage reaction is 1:0.7. The catalyst carbon formation is shown in Table 3.
[0030] Table 3. Data table of heat transfer and carbon deposition between two bed sections
[0031]
PUM
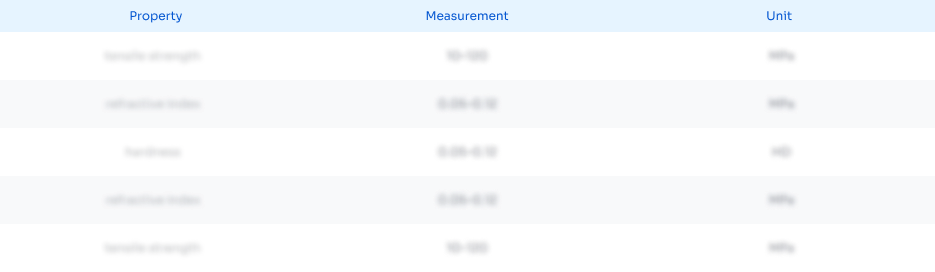
Abstract
Description
Claims
Application Information

- R&D
- Intellectual Property
- Life Sciences
- Materials
- Tech Scout
- Unparalleled Data Quality
- Higher Quality Content
- 60% Fewer Hallucinations
Browse by: Latest US Patents, China's latest patents, Technical Efficacy Thesaurus, Application Domain, Technology Topic, Popular Technical Reports.
© 2025 PatSnap. All rights reserved.Legal|Privacy policy|Modern Slavery Act Transparency Statement|Sitemap|About US| Contact US: help@patsnap.com