Vacuum auxiliary molding technique produced by high-facade composite material for ship
A composite material and forming process technology, applied in the field of composite material forming process, can solve the problems such as the absence of patents for vacuum-assisted forming process methods for high-facade composite material parts, incomplete impregnation of reinforcing materials, and affecting the quality of parts, etc., to achieve The appearance is uniform and beautiful in color, less defects, and the effect of marine environment resistance
- Summary
- Abstract
- Description
- Claims
- Application Information
AI Technical Summary
Problems solved by technology
Method used
Image
Examples
Embodiment 1
[0041] Formula: (parts by mass)
[0042]Vinyl ester resin (430LV) 100 parts
[0043] 2 parts methyl ethyl ketone peroxide (MEKP M-50)
[0044] Cobalt naphthenate (accelerator E) 0.8 parts
[0045] Release agent: solution type release agent (700NC).
[0046] Equipment: RCD vacuum-assisted forming equipment is used.
[0047] Mold treatment: use solution-type release agent (700NC) to treat the surface of the mold, and the thickness is controlled at 0.05-0.4mm.
[0048] Reinforcement material: Cut high-strength glass fiber fabrics of appropriate size according to the lay-up design and runner design.
[0049] Lamination: Lay high-strength glass fiber fabrics according to the design of orthogonal lamination.
[0050] Release cloth laying: According to the size of the product, the release cloth of the corresponding size is cut and spread on the surface of the high-strength glass fiber fabric, and attention should be paid to avoid bubbling and pleating
[0051] Pipeline and dive...
PUM
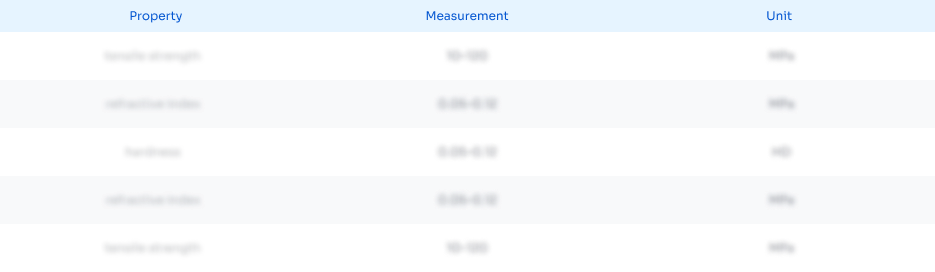
Abstract
Description
Claims
Application Information

- R&D
- Intellectual Property
- Life Sciences
- Materials
- Tech Scout
- Unparalleled Data Quality
- Higher Quality Content
- 60% Fewer Hallucinations
Browse by: Latest US Patents, China's latest patents, Technical Efficacy Thesaurus, Application Domain, Technology Topic, Popular Technical Reports.
© 2025 PatSnap. All rights reserved.Legal|Privacy policy|Modern Slavery Act Transparency Statement|Sitemap|About US| Contact US: help@patsnap.com