Method for separating main ingredients of arboret stalk by low-intensity steam explosion
A low-intensity, steam technology, applied in biofuels, fermentation and other directions, can solve the problems of high pressure resistance and other performance requirements of pressure maintenance time equipment, less than 50% utilization rate of lignocellulosic raw materials, and inability to make full use of it. Achieve high-value utilization, reduce extraction and separation costs, and be easy to recycle
- Summary
- Abstract
- Description
- Claims
- Application Information
AI Technical Summary
Problems solved by technology
Method used
Image
Examples
Embodiment 1
[0035] The air-dried stalks of Huzhizi are removed from impurities and chips, and the size of the material is less than 30mm×5mm×5mm (length, width, thickness); then divided into two groups: the experimental group and the control group, and the experimental group is subjected to low-intensity steam explosion, and the steam explosion pressure is 0.8 MPa, pressure maintenance time is 60 seconds; the control group does not undergo steam explosion, the steam explosion product of the experimental group and the material of the control group are respectively ground by a disc mill; The elemental components are subjected to pressurized rapid extraction and separation. The weight ratio of water and blasting materials is 15:1. The pressurization is carried out for 5 minutes during the extraction, and the pressurization is stopped for 5 minutes. The maximum pressure of the pressurization is 0.2MPa. The polysulfone membrane with a molecular weight of 2000 is used to intercept and separate h...
Embodiment 2
[0044] Air-dried Salix stalks remove impurities and shavings, the size of the material is less than 30mm×10mm×10mm (length, width, thickness), steam explosion pressure is 0.9MPa, and the pressure maintenance time is 120 seconds for steam explosion; the steam explosion product is ground by a disc mill crushing; use warm water at 55°C as solvent to carry out pressurized rapid extraction and separation of hemicellulose components, the weight ratio of water and blasting materials is 15:1, pressurize for 10 minutes during extraction, stop pressurization for 10 minutes, and the maximum pressure of pressurization is 0.3 MPa, circulating for 1.5 hours, the extract was separated by ultrafiltration with a polysulfone membrane with a molecular weight cut-off of 2000, and the hemicellulose was separated. After ultrafiltration and concentration, the water was recycled, and the concentrate was dried to obtain hemicellulose. The hemicellulose extraction rate was 89.6%.
[0045] The solid resi...
Embodiment 3
[0048] Air-dried caragana stems are removed and shavings, the material size is less than 30mm×10mm×10mm (length, width, thickness); the steam explosion pressure is 0.7MPa, and the pressure maintenance time is 60 seconds for steam explosion; the steam explosion product is ground by a disc mill crushing; use warm water at 50°C as solvent to extract and separate the hemicellulose components quickly under pressurization, the weight ratio of water and blasting materials is 15:1, pressurize for 5 minutes during extraction, stop pressurizing for 5 minutes, and the maximum pressure of pressurization is 0.1 MPa, circulated for 1 hour, the extract was separated by ultrafiltration with a polysulfone membrane with a molecular weight cut-off of 2000, and the hemicellulose was separated. After ultrafiltration and concentration, the water was recycled, and the concentrate was dried to obtain hemicellulose. The hemicellulose extraction rate was 85.7%.
[0049] The solid residue after hemicellu...
PUM
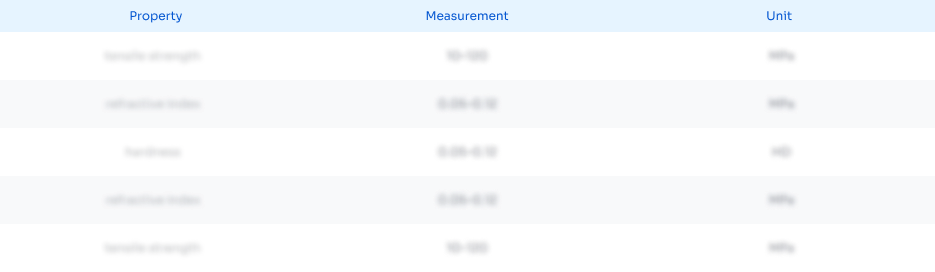
Abstract
Description
Claims
Application Information

- Generate Ideas
- Intellectual Property
- Life Sciences
- Materials
- Tech Scout
- Unparalleled Data Quality
- Higher Quality Content
- 60% Fewer Hallucinations
Browse by: Latest US Patents, China's latest patents, Technical Efficacy Thesaurus, Application Domain, Technology Topic, Popular Technical Reports.
© 2025 PatSnap. All rights reserved.Legal|Privacy policy|Modern Slavery Act Transparency Statement|Sitemap|About US| Contact US: help@patsnap.com