Method and equipment for comprehensive treatment of waste water and waste gas in viscose fiber preparation
A viscose fiber and comprehensive treatment technology, which is applied in the field of waste water and waste gas treatment in viscose fiber production, to achieve the effects of reducing emissions, reducing hydrogen sulfide and carbon disulfide emissions, and reducing pollution
- Summary
- Abstract
- Description
- Claims
- Application Information
AI Technical Summary
Problems solved by technology
Method used
Image
Examples
Embodiment 1
[0061] A. Collect the waste lye from the raw hydraulic pressing process in viscose fiber production, filter out cellulose and hemicellulose, and enter the absorption tank from the top in the form of jet flow.
[0062] B. The process waste gas containing hydrogen sulfide and carbon disulfide is sent from the air duct to the absorption tank through the fan and enters in the form of ring pipe aeration. The alkali concentration of the lye absorption liquid is 150 g / liter, and the gas-liquid ratio is 100:1 / minutes (that is, the lye spray speed is 1.67m 3 / min, the insufficient part is supplemented by reflux lye).
[0063] C. The hydrogen sulfide concentration in the process waste gas is 70g / m 3 , carbon disulfide concentration 6.4g / m 3 The spent alkali and exhaust gas are fully mixed in the absorption tank to make a neutralizing liquid, the hydrogen sulfide in it reacts with the sodium hydroxide in the spent alkali to form sodium sulfide or sodium hydrogen sulfide dissolved in t...
Embodiment 2
[0068] A. Collect the waste lye from the raw hydraulic pressing process in viscose fiber production, filter out cellulose and hemicellulose, and enter the absorption tank from the top in the form of jet flow.
[0069] B. The process waste gas containing hydrogen sulfide and carbon disulfide is sent from the air duct to the absorption tank through the fan and enters in the form of ring pipe aeration. The alkali concentration of the lye absorption liquid is 180 g / liter, and the gas-liquid ratio is 100:1 / minutes (that is, the lye spray speed is 1.67m 3 / min, the insufficient part is supplemented by reflux lye).
[0070] C. The concentration of hydrogen sulfide in the process waste gas is 75g / m 3 , carbon disulfide concentration 7g / m 3 The spent alkali and exhaust gas are fully mixed in the absorption tank to make a neutralizing liquid, the hydrogen sulfide in it reacts with the sodium hydroxide in the spent alkali to form sodium sulfide or sodium hydrogen sulfide dissolved in ...
Embodiment 3
[0075] A. Collect the waste lye from the raw hydraulic pressing process in viscose fiber production, filter out cellulose and hemicellulose, and enter the absorption tank from the top in the form of jet flow.
[0076] B. The process waste gas containing hydrogen sulfide and carbon disulfide is sent from the air duct to the absorption tank through the fan and enters in the form of ring pipe aeration. The alkali concentration of the lye absorption liquid is 200 g / liter, and the gas-liquid ratio is 100:1 / minutes (that is, the lye spray speed is 1.67m 3 / min, the insufficient part is supplemented by reflux lye).
[0077] C. The hydrogen sulfide concentration in the process waste gas is 70g / m 3 , carbon disulfide concentration 7g / m 3 The spent alkali and exhaust gas are fully mixed in the absorption tank to make a neutralizing liquid, the hydrogen sulfide in it reacts with the sodium hydroxide in the spent alkali to form sodium sulfide or sodium hydrogen sulfide dissolved in the...
PUM
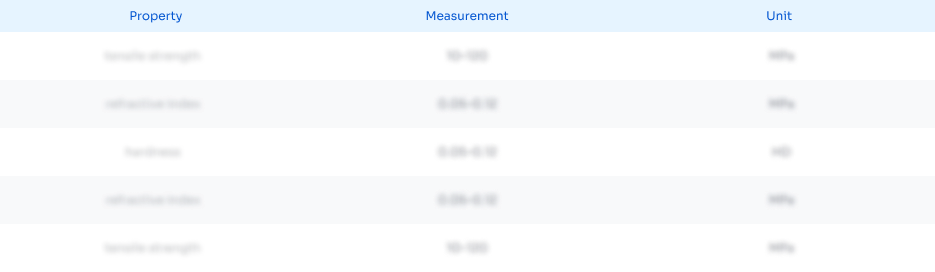
Abstract
Description
Claims
Application Information

- R&D
- Intellectual Property
- Life Sciences
- Materials
- Tech Scout
- Unparalleled Data Quality
- Higher Quality Content
- 60% Fewer Hallucinations
Browse by: Latest US Patents, China's latest patents, Technical Efficacy Thesaurus, Application Domain, Technology Topic, Popular Technical Reports.
© 2025 PatSnap. All rights reserved.Legal|Privacy policy|Modern Slavery Act Transparency Statement|Sitemap|About US| Contact US: help@patsnap.com