Method for enhancing performance of electric heating tube
An electric heating tube, performance technology, applied in the direction of the heating element shape, etc., can solve the problem that the high temperature resistance and high temperature corrosion resistance of the stainless steel tube cannot be improved, and achieve the elimination of internal stress and surface hardening state, easy deformation of the bent tube, and increase the high temperature performance effect
- Summary
- Abstract
- Description
- Claims
- Application Information
AI Technical Summary
Problems solved by technology
Method used
Examples
Embodiment 1
[0017] Example 1: outer diameter The stainless steel pipe made of 304 (Ocr18Ni9) is used as the outer pipe of the electric heating pipe, and the electric heating wire is penetrated and filled with magnesium oxide powder, and then the conventional shrinkage treatment is performed; after the treatment, the semi-finished product is subjected to high-temperature bright treatment by using a protective atmosphere mesh belt high-temperature furnace; After high-temperature bright treatment, pipe bending is performed to form "U-shaped", "W-shaped" and other shapes; the semi-finished product after bending is subjected to a second high-temperature bright treatment; after the second high-temperature bright treatment, the outer tube is not completely cooled Drop silicone oil into the nozzle to initially seal the nozzle. Some parameters of the two high-temperature brightening treatments are as follows:
[0018] 1) Protective atmosphere: pass through ammonia gas, decompose into N 2 and H ...
Embodiment 2
[0021] Embodiment 2, outer diameter The stainless steel pipe made of 310S (Ocr25Ni20) is used as the outer pipe of the electric heating pipe, and the electric heating wire is penetrated and filled with magnesium oxide powder to perform conventional shrinkage treatment; after the treatment, the semi-finished product is subjected to high-temperature oxidation treatment in a protective atmosphere mesh belt high-temperature furnace; After the high-temperature oxidation treatment, pipe bending is performed to form "U-shaped", "W-shaped" and other shapes; the semi-finished products after bending are subjected to conventional moisture removal treatment; after the moisture removal treatment, before the outer pipe is completely cooled, drip Fill in the silicone oil to initially seal the nozzle. Some parameters of high temperature oxidation treatment are as follows:
[0022] 1) Protection and control atmosphere: formed by burning, condensing and drying air and liquefied petroleum gas,...
PUM
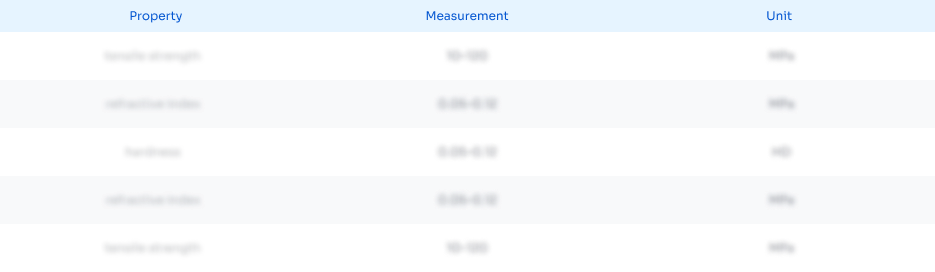
Abstract
Description
Claims
Application Information

- R&D Engineer
- R&D Manager
- IP Professional
- Industry Leading Data Capabilities
- Powerful AI technology
- Patent DNA Extraction
Browse by: Latest US Patents, China's latest patents, Technical Efficacy Thesaurus, Application Domain, Technology Topic, Popular Technical Reports.
© 2024 PatSnap. All rights reserved.Legal|Privacy policy|Modern Slavery Act Transparency Statement|Sitemap|About US| Contact US: help@patsnap.com