AIN film preparing method
A technology of thin film and epitaxial thin film, which is applied in the field of preparation of AlN thin film, can solve the problems of low dislocation density AlN thin film, etc.
- Summary
- Abstract
- Description
- Claims
- Application Information
AI Technical Summary
Problems solved by technology
Method used
Image
Examples
preparation example Construction
[0018] A method for preparing an AlN thin film, characterized in that:
[0019] 1.1 In the epitaxial film growth chamber, Al 2 0 3 , SiC or Si is the substrate 3, and the substrate 3 is nitrided at a temperature of 800-850° C. for 10-30 minutes;
[0020] 1.2. A 10-20nm AlN (aluminum nitride) buffer layer 4 is grown at 500-765°C;
[0021] 1.3. Growing the AlN epitaxial layer 1 in an environment greater than 780°C;
[0022] 1.4. In the process of growing the AlN epitaxial layer 1, every time the AlN epitaxial layer 1 grows 100-500 nm, a layer of 10-20 nm AlN insertion layer 2 is grown at 500-765 ° C, and the growth interruption method is used to interrupt the AlN grow for 0.5-3 minutes, and then continue to grow the AlN epitaxial layer 1 in an environment greater than 780° C., repeating this cycle until the required number of layers is obtained.
[0023] Moreover, the number of AlN insertion layers 2 is 3 to 8 layers.
[0024] Moreover, the AlN buffer layer 4 is grown by pu...
Embodiment 1
[0028] Select two inches of Al 2 o 3 As the substrate 3, the substrate 3 was cleaned at 810° C. for 10 minutes before growth. Nitriding the substrate 3 at 800°C for 10 minutes, then growing a 10nm AlN buffer layer 4 at 500°C, and then growing a 1.8μm AlN epitaxial layer 1 at 780°C; in the process of growing the AlN epitaxial layer 1 In this method, for every 100nm AlN epitaxial layer growth, a 10nm AlN insertion layer 2 was grown at 500°C, and the AlN growth was interrupted for 0.5 minutes, and then the AlN epitaxial layer 1 was continued to grow at 800°C.
Embodiment 2
[0030] Two inches of Si was selected as the substrate 3, and the substrate 3 was cleaned at 810°C for 10 minutes before growth. Nitriding the substrate 3 at 850°C for 30 minutes, then growing a 20nm AlN buffer layer 4 at 765°C, and then growing a 1.8μm AlN epitaxial layer 1 at 800°C; during the process of growing the AlN epitaxial layer 1 , every time a 500nm AlN epitaxial layer is grown, a 20nm AlN insertion layer 2 is grown at 765°C, and the AlN growth is interrupted for 3 minutes, and then the AlN epitaxial layer 1 is grown at 800°C, and the number of AlN insertion layers 2 is 8 floors.
PUM
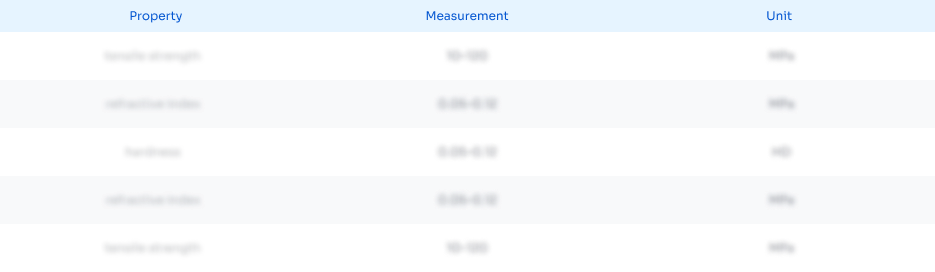
Abstract
Description
Claims
Application Information

- R&D Engineer
- R&D Manager
- IP Professional
- Industry Leading Data Capabilities
- Powerful AI technology
- Patent DNA Extraction
Browse by: Latest US Patents, China's latest patents, Technical Efficacy Thesaurus, Application Domain, Technology Topic, Popular Technical Reports.
© 2024 PatSnap. All rights reserved.Legal|Privacy policy|Modern Slavery Act Transparency Statement|Sitemap|About US| Contact US: help@patsnap.com