Axial gap type eccentric rotor and axial gap type coreless vibrating motor using said rotor
An eccentric rotor and gap-type technology, which is applied in the direction of electric components, fluids using vibration, electrical components, etc., can solve the problems that it is difficult to ensure the impact resistance strength of the eccentric hammer, and achieve the effect of preventing falling off and ensuring impact resistance
- Summary
- Abstract
- Description
- Claims
- Application Information
AI Technical Summary
Problems solved by technology
Method used
Image
Examples
Embodiment 1
[0029] As the axial gap type rotor of the present invention, a rotor composed of an eccentric rotor for generating vibration will be described here.
[0030] In FIGS. 1 to 3 , a printed circuit board 1 made of a glass fiber cloth epoxy substrate is formed in an expanded fan shape, and a bearing 2 as a shaft support is arranged in the center. A six-pole sector land (land) 1s is formed on one surface side of the outside of the bearing 2 , and the converter C is formed by plating several micrometers of gold on the surface. The segment lands 1 s of the converter are connected to each other by a short-circuited wire land 1 k via vias 1 h. Three long holes 1t are formed on the outside to the inner diameter of the winding so that the winding start ends a, b, and c of the wire-wound hollow armature windings 3A, 3B, and 3C described later can be safely drawn out. On the other side of the printed circuit board 1, a wire bonding area is formed through a through hole 1h to short-circuit ...
Embodiment 2
[0036] Fig. 4 shows a modified example of the eccentric rotor. In order to increase the thickness of the wire-wound hollow armature winding in a limited gap to increase the output, and to achieve long life as a converter, the segments 13 of the converter are set at The thicker flat plate type with precious metal cladding on the surface, that is, the printed circuit board 11 is arranged inside these wire-wound type hollow armature windings in such a way that it does not overlap with the hollow armature winding 33, and the sector pieces 13 are soldered fixed on one surface. During this soldering, the positions of the respective wiring lands are re-determined, the solder lands are ensured, and the printed circuit board 11 is directly soldered on the inner side of the flat sliding joint. In this way, the segment piece 13 of the converter can be substantially set so as not to protrude from the lower surface of the rotor, and the sliding flexing stroke of the brush can be sufficient...
PUM
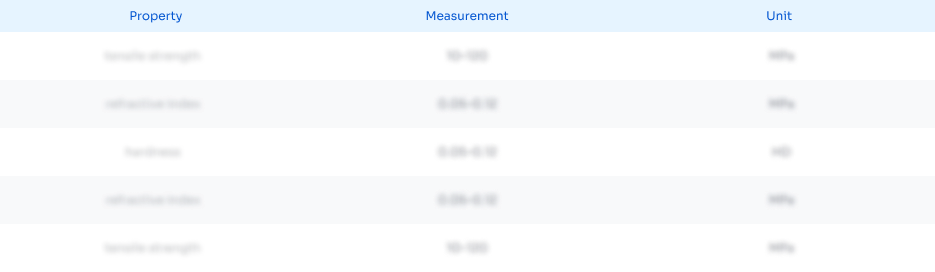
Abstract
Description
Claims
Application Information

- R&D
- Intellectual Property
- Life Sciences
- Materials
- Tech Scout
- Unparalleled Data Quality
- Higher Quality Content
- 60% Fewer Hallucinations
Browse by: Latest US Patents, China's latest patents, Technical Efficacy Thesaurus, Application Domain, Technology Topic, Popular Technical Reports.
© 2025 PatSnap. All rights reserved.Legal|Privacy policy|Modern Slavery Act Transparency Statement|Sitemap|About US| Contact US: help@patsnap.com