Hot edge-cutting manufacture technology for automobile generator finish forging claw pole
A manufacturing process and precision forging technology, applied in the field of red trimming manufacturing process, can solve the problems of large initial investment, high product shear strength and high logistics cost, and achieve the effects of improving service life, appearance quality control and product quality.
- Summary
- Abstract
- Description
- Claims
- Application Information
AI Technical Summary
Problems solved by technology
Method used
Image
Examples
Embodiment Construction
[0031] The present invention will now be described in further detail in conjunction with the accompanying drawings and preferred embodiments. These drawings are all simplified schematic diagrams, which only illustrate the basic structure of the present invention in a schematic manner, so they only show the configurations related to the present invention.
[0032] Such as Figure 1-2 The claw pole of the automobile generator shown in the present invention has a bottom plate 1, six beak-shaped claws 2 are evenly distributed on the bottom plate 1, a yoke 3 is arranged in the middle of the bottom plate 1, and on the circumference of the yoke 3 Six insulating varnish drainage grooves 4 are evenly distributed, and six coil anti-rotation protrusions 5 and six lead-out grooves 6 for insulating wires are distributed on the bottom of the yoke 3 .
[0033] Such as image 3 The red trimming manufacturing process of the precision forged claw pole of the automobile generator shown in the ...
PUM
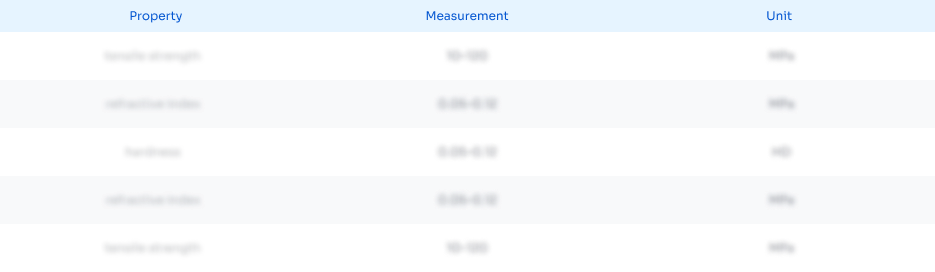
Abstract
Description
Claims
Application Information

- Generate Ideas
- Intellectual Property
- Life Sciences
- Materials
- Tech Scout
- Unparalleled Data Quality
- Higher Quality Content
- 60% Fewer Hallucinations
Browse by: Latest US Patents, China's latest patents, Technical Efficacy Thesaurus, Application Domain, Technology Topic, Popular Technical Reports.
© 2025 PatSnap. All rights reserved.Legal|Privacy policy|Modern Slavery Act Transparency Statement|Sitemap|About US| Contact US: help@patsnap.com