High temperature phosphorization process of stone oil drill collar screwed nipple
A threaded joint and oil drilling technology, which is applied in the coating process of metal materials, etc., can solve the problems of slow crystallization of phosphating grains, insufficient ion adhesion, and large pores
- Summary
- Abstract
- Description
- Claims
- Application Information
AI Technical Summary
Problems solved by technology
Method used
Examples
Embodiment Construction
[0019] The present invention will be further illustrated below by specific examples.
[0020] The high-temperature phosphating process for threaded joints of petroleum drill collars includes three processes: pre-phosphating surface treatment, high-temperature phosphating treatment and post-phosphating surface treatment. This embodiment firstly implements the surface treatment process before phosphating: place the drill collar to be treated obliquely on the station frame, the threaded joint of the drill collar is at the bottom end, apply degreaser on the thread and shoulder, and after 1~ 2-minute degreasing treatment to remove the grease adhered during machining. Then rinse the degreaser attached to the threaded joint of the drill collar with clean water. The second step is to implement high-temperature phosphating treatment process: put the phosphating solution with a total content of 18% in an open container and heat it to 90±2°C, move the open container containing the phosp...
PUM
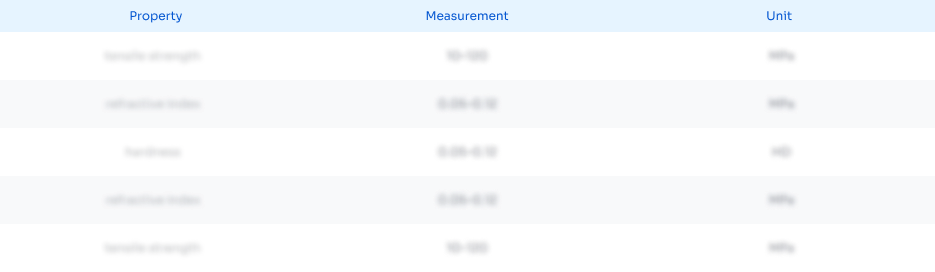
Abstract
Description
Claims
Application Information

- Generate Ideas
- Intellectual Property
- Life Sciences
- Materials
- Tech Scout
- Unparalleled Data Quality
- Higher Quality Content
- 60% Fewer Hallucinations
Browse by: Latest US Patents, China's latest patents, Technical Efficacy Thesaurus, Application Domain, Technology Topic, Popular Technical Reports.
© 2025 PatSnap. All rights reserved.Legal|Privacy policy|Modern Slavery Act Transparency Statement|Sitemap|About US| Contact US: help@patsnap.com