Flue gas waste heat recovery system of metallurgy electric furnace
A flue gas waste heat recovery system technology, applied in preheating, feed water heaters, lighting and heating equipment, etc., can solve the problems of low hot water taste and low utilization efficiency, and achieve the effect of improving utilization efficiency and good utilization
- Summary
- Abstract
- Description
- Claims
- Application Information
AI Technical Summary
Problems solved by technology
Method used
Image
Examples
Embodiment Construction
[0010] Preferred embodiments of the present invention will be described below with reference to the drawings.
[0011] Such as figure 1 As shown, the flue gas discharged from the electric furnace 1 is introduced into the waste heat boiler 4 provided outside the electric furnace 1 . The waste heat boiler 4 is provided with an evaporative heating surface 5 and an economizer 6. During the process of flowing through the evaporating heating surface 5 and the economizer 6, the flue gas conducts convective heat exchange with the water flowing therein, so that the heat is recovered, and the temperature reduce. Both the evaporation heating surface 5 and the economizer 6 adopt known structures, and their detailed descriptions are omitted here.
[0012] Furthermore, a steam drum 3 is provided on the top of the waste heat boiler 4, and the structure of the steam drum 3 is also known, so its detailed description will be omitted here. The steam drum 3 is connected to the outlet of the ec...
PUM
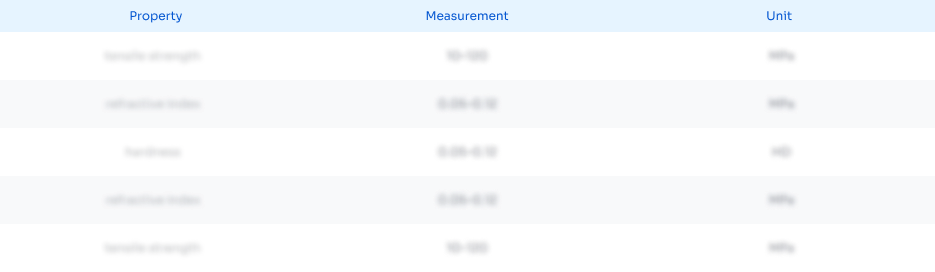
Abstract
Description
Claims
Application Information

- R&D Engineer
- R&D Manager
- IP Professional
- Industry Leading Data Capabilities
- Powerful AI technology
- Patent DNA Extraction
Browse by: Latest US Patents, China's latest patents, Technical Efficacy Thesaurus, Application Domain, Technology Topic, Popular Technical Reports.
© 2024 PatSnap. All rights reserved.Legal|Privacy policy|Modern Slavery Act Transparency Statement|Sitemap|About US| Contact US: help@patsnap.com