Patassium dihydrogen phosphate crystal slaking and finishing method
A technology of potassium dihydrogen phosphate and crystal, applied in the field of deliquescence polishing of potassium dihydrogen phosphate crystal, can solve the problems of difficult cleaning of polishing liquid, removal of abrasive grains, low processing efficiency, etc., and achieves novel method, easy cleaning and high processing efficiency. Effect
- Summary
- Abstract
- Description
- Claims
- Application Information
AI Technical Summary
Problems solved by technology
Method used
Image
Examples
specific Embodiment approach 1
[0021] Specific implementation mode one: combine figure 1 The present embodiment will be described. The steps of the polishing method of the present embodiment are as follows:
[0022] Step 1. The KDP crystal polishing device is composed of a polishing pad 1, a deliquescent polishing liquid dripper 2, a polishing disc 3 and a sample loading disc 5. The polishing pad 1 is set on the upper surface of the polishing disc 3, and the sample loading disc 5 is set on the polishing pad Above the optical disk 3, the sample loading disk 5 and the polishing disk 3 are respectively connected with the rotating mechanism and arranged facing each other;
[0023] Step 2, fixing the KDP crystal 4 blank on the bottom end surface of the sample loading tray 5, and using the existing cutting technology to pretreat the surface to be polished of the KDP crystal 4 blank;
[0024] Step 3, activate the pressure control switch to apply pressure longitudinally to the sample tray 5, and the pressure valu...
specific Embodiment approach 2
[0027] Specific implementation mode two: combination figure 2 The present embodiment will be described. The steps of the polishing method of the present embodiment are as follows:
[0028] Step 1, the KDP crystal polishing device is composed of a polishing pad 1, a polishing disc 3, a sample loading disc 5, a sealing cover 6, a water vapor input pipeline 7 and a water vapor recovery pipeline 8, and the polishing pad 1 is arranged on the upper surface of the polishing disc 3 , the sample loading tray 5 is arranged on the top of the polishing tray 3, the water vapor input pipeline 7 is arranged on the upper right side of the sealing cover 6, the water vapor recovery pipeline 8 is arranged on the lower left side of the sealing cover 6, the sample loading tray 5 and the polishing tray 3 are respectively It is connected with the rotating mechanism and arranged opposite to each other;
[0029] Step 2, fixing the KDP crystal 4 blank on the bottom end surface of the sample loading ...
specific Embodiment approach 3
[0033] Embodiment 3: In step 3 of this embodiment, when the size of the surface of the KDP crystal to be polished is 18 mm×12 mm, the longitudinal pressure applied to the sample loading plate 5 is 0.14 MPa.
PUM
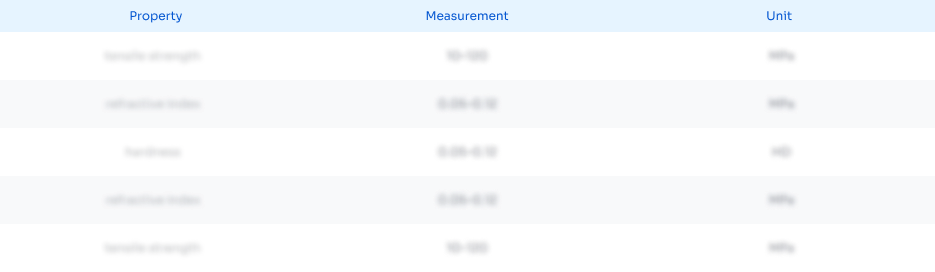
Abstract
Description
Claims
Application Information

- R&D Engineer
- R&D Manager
- IP Professional
- Industry Leading Data Capabilities
- Powerful AI technology
- Patent DNA Extraction
Browse by: Latest US Patents, China's latest patents, Technical Efficacy Thesaurus, Application Domain, Technology Topic, Popular Technical Reports.
© 2024 PatSnap. All rights reserved.Legal|Privacy policy|Modern Slavery Act Transparency Statement|Sitemap|About US| Contact US: help@patsnap.com