Method for preparing graphitic centrifugal pump spiral casing
A technology of centrifugal pump and pump casing, which is applied to parts, pumps, pump elements, etc. of pumping devices for elastic fluids to achieve the effect of mass production and low cost
- Summary
- Abstract
- Description
- Claims
- Application Information
AI Technical Summary
Problems solved by technology
Method used
Image
Examples
Embodiment Construction
[0012] The specific implementation of the present invention is described below:
[0013] 1) Select high-strength graphite material as the graphite pump casing blank, such as Figure 1 to Figure 4 As shown, the main body 1 of the pump casing is processed first, and the specific method is as follows:
[0014] A Machining A light hole 4 with a diameter of φ131mm at the center of the spiral flow channel to be processed;
[0015] B Turn out a threaded hole 6 with an inner diameter of φ240mm and a depth of 30mm on the back of the blank corresponding to the light hole 4 of A; because the threaded hole 6 is larger than the maximum radius of the spiral flow channel 3, after the threaded hole 6 is processed, the spiral flow channel 3 The processing environment is open, and there is no undercurrent channel 9, so the spiral flow channel 3 can be processed by numerical control machining and general machining;
[0016] C processing inner diameter is the outlet port 8 of the vortex flow pa...
PUM
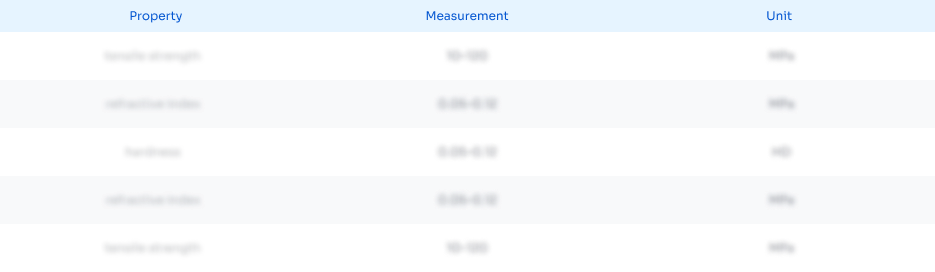
Abstract
Description
Claims
Application Information

- R&D
- Intellectual Property
- Life Sciences
- Materials
- Tech Scout
- Unparalleled Data Quality
- Higher Quality Content
- 60% Fewer Hallucinations
Browse by: Latest US Patents, China's latest patents, Technical Efficacy Thesaurus, Application Domain, Technology Topic, Popular Technical Reports.
© 2025 PatSnap. All rights reserved.Legal|Privacy policy|Modern Slavery Act Transparency Statement|Sitemap|About US| Contact US: help@patsnap.com