Compression sintering and quenching integrated production process for cemented carbides
A pressure sintering and production process technology, applied in the field of cemented carbide production process, can solve the problems of high consumption of inert gas, low product strength, large equipment investment, etc., and achieve the effects of improving production efficiency, reducing energy consumption and reducing production costs
- Summary
- Abstract
- Description
- Claims
- Application Information
AI Technical Summary
Problems solved by technology
Method used
Image
Examples
Embodiment Construction
[0010] The pressure sintering and quenching integrated furnace consists of furnace body 1, heat insulation screen 2, pushing mechanism 3, electric heating element 5, argon gas channel 6, argon gas channel 8, vacuum pressure valve 9, vacuum pressure valve 10, fan housing 11. Fan 12, heat exchanger 13, product boat support box 14, temperature measurement and control thermocouple 15 (see figure 1 ); front and rear doors 1-1 of the furnace body and a rear door 1-2 of the furnace body are respectively arranged at the front and rear ends of the furnace body 1, the thermal insulation screen 2 is installed in the furnace body 1, and the electric heating element 5 is installed in the thermal insulation screen 2 , the product boat bracket box 14 is installed in the furnace body 1, and the front and rear doors 2-1 and 2-2 of the heat insulation screen are respectively provided at the front and rear ends of the heat insulation screen 2, and the pushing mechanism 3 is installed on the furna...
PUM
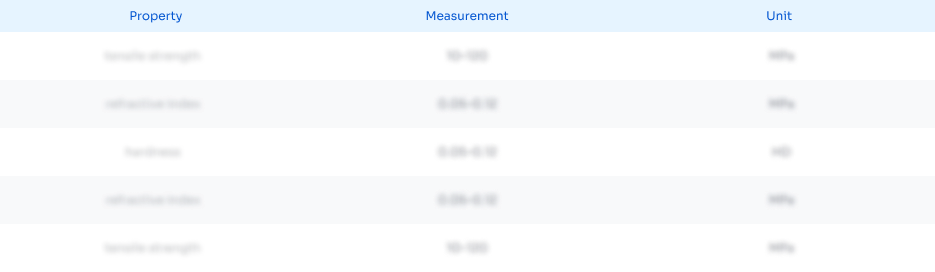
Abstract
Description
Claims
Application Information

- R&D
- Intellectual Property
- Life Sciences
- Materials
- Tech Scout
- Unparalleled Data Quality
- Higher Quality Content
- 60% Fewer Hallucinations
Browse by: Latest US Patents, China's latest patents, Technical Efficacy Thesaurus, Application Domain, Technology Topic, Popular Technical Reports.
© 2025 PatSnap. All rights reserved.Legal|Privacy policy|Modern Slavery Act Transparency Statement|Sitemap|About US| Contact US: help@patsnap.com