Method for shortening sintering time of resistant material of electric furnace at time of opening new furnace
A sintering time and new furnace technology, applied in the field of electric furnace smelting, can solve the problems of increasing the production cost of smelting power consumption, shortening the sintering time of the electric furnace refractory material, unfavorable energy saving and consumption reduction of the electric furnace, etc. The effect of saving oven time
- Summary
- Abstract
- Description
- Claims
- Application Information
AI Technical Summary
Problems solved by technology
Method used
Examples
Embodiment
[0016] Embodiment: applicant Suzhou Iron and Steel Group Electric Furnace Factory, the electric furnace furnace type that adopts: 100DC EBT6.6 / 100, the inner diameter of lower furnace shell of this 100 tons electric furnace is 6500mm, bottom shell radius 7850mm, furnace shell capacity 115t; Use bagged calcined oil Coke carburizer: fixed carbon ≥ 98.5%, sulfur ≤ 0.5%, ash ≤ 0.5%), 20 kg of petroleum coke carburizer per bag.
[0017] Before starting the production of the first furnace of a new furnace, prepare spare electric furnace refractory materials according to the normal furnace construction process, and then pack the above-mentioned bagged calcined petroleum coke carburizer evenly on the slope of the rammed furnace bottom. The average laying thickness is about 30mm, the laying amount is basically about 180 kg / square meter, and the consumption is about 5 tons.
[0018] When opening a new furnace, 3 baskets of scrap steel are made, and hot metal is normally hot-charged. Aft...
PUM
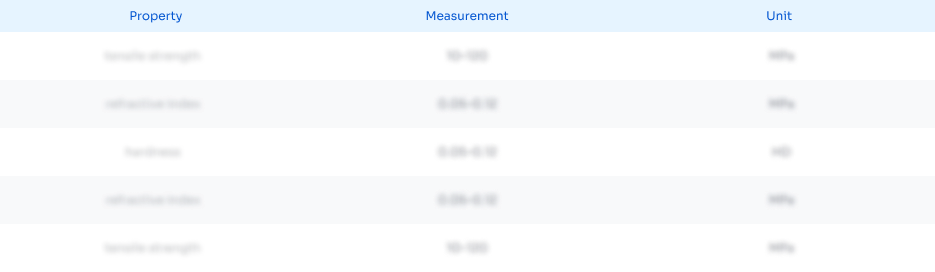
Abstract
Description
Claims
Application Information

- R&D
- Intellectual Property
- Life Sciences
- Materials
- Tech Scout
- Unparalleled Data Quality
- Higher Quality Content
- 60% Fewer Hallucinations
Browse by: Latest US Patents, China's latest patents, Technical Efficacy Thesaurus, Application Domain, Technology Topic, Popular Technical Reports.
© 2025 PatSnap. All rights reserved.Legal|Privacy policy|Modern Slavery Act Transparency Statement|Sitemap|About US| Contact US: help@patsnap.com