High heat-resistant rubber composite material for conveyor belt covering
A technology of composite materials and conveyor belts, which is applied in the direction of conveyors, transportation and packaging, etc., can solve the problems of affecting the service life of conveyor belts, poor self-adhesion and mutual adhesion, and low bonding strength between skeleton layer materials and covering layers, and achieves Excellent anti-aging cracking performance, good heat aging resistance, excellent mechanical properties and the effect of wear resistance
- Summary
- Abstract
- Description
- Claims
- Application Information
AI Technical Summary
Problems solved by technology
Method used
Image
Examples
Embodiment 1
[0025] Embodiment 1: on the two-roll mill, add 100g EPDM rubber (commercially available EPDM1705) masticate, then add activator successively: zinc oxide 4g, magnesium oxide 2g and stearic acid 1g, N-4 (aniline Base phenyl) methacrylamide (NAPM) 2g, tackifier: magnesium methacrylate 10g, reinforcing carbon black: 60g, plasticizer: low molecular weight polybutadiene 10g, finally add cross-linking agent and cross-crossing aid Joint agent: 5 g of dicumyl peroxide (DCP) and 0.2 g of sulfur, and mix them uniformly on an open mill to obtain a rubber compound. The rubber compound was vulcanized at 160 °C to obtain a rubber composite. The mechanical properties, adhesive strength and wear resistance before and after aging are shown in Table 1.
Embodiment 2
[0026] Embodiment 2: On the two-roll mill, add 20g EPDM rubber (EPDM1705) and 80g ethylene-butylene copolymerized elastomer masticate, then add activator successively: zinc oxide 4g, magnesium oxide 8g and stearic acid 1g, N-4 (anilinophenyl) maleimide (MC) 2g, tackifier: zinc methacrylate 20g, reinforcing carbon black: 60g, plasticizer: low molecular weight polybutadiene 20g, Finally add cross-linking agent and co-cross-linking agent: 2,5-dimethyl-2,5-di-tert-butylperoxyhexane (double 25) 10g and sulfur 0.2g, mix uniformly on an open mill to obtain a rubber compound . The rubber compound was vulcanized at 160 °C to obtain a rubber composite. The mechanical properties, adhesive strength and wear resistance before and after aging are shown in Table 1.
Embodiment 3
[0027] Embodiment 3: On the two-roll mill, add 100g ethylene-octene copolymer elastomer (commercially available POE8180) masticate, then add activator successively: Zinc oxide 4g, magnesium oxide 12g and stearic acid 1g, N-4 (anilinophenyl) methacrylamide (NAPM) 4g, tackifier: magnesium methacrylate 20g, reinforcing carbon black: 60g, plasticizer: low molecular weight ethylene propylene copolymer 20g, finally add crosslinking agent and Auxiliary cross-linking agent: 14 g of benzoyl peroxide (BP) and 0.2 g of sulfur, mixed uniformly on an open mill to obtain a rubber compound. The rubber compound was vulcanized at 160 °C to obtain a rubber composite. The mechanical properties, adhesive strength and wear resistance before and after aging are shown in Table 1.
PUM
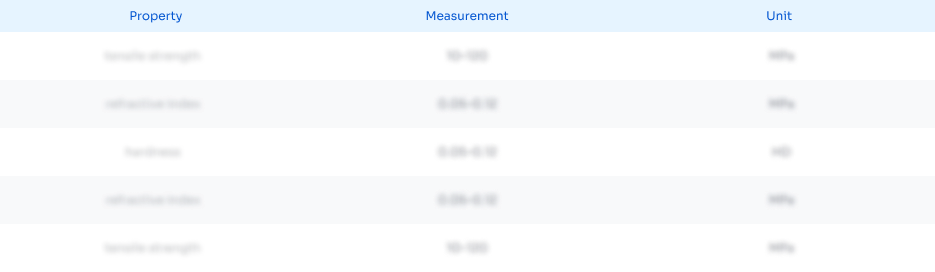
Abstract
Description
Claims
Application Information

- Generate Ideas
- Intellectual Property
- Life Sciences
- Materials
- Tech Scout
- Unparalleled Data Quality
- Higher Quality Content
- 60% Fewer Hallucinations
Browse by: Latest US Patents, China's latest patents, Technical Efficacy Thesaurus, Application Domain, Technology Topic, Popular Technical Reports.
© 2025 PatSnap. All rights reserved.Legal|Privacy policy|Modern Slavery Act Transparency Statement|Sitemap|About US| Contact US: help@patsnap.com