Roll forming integrated technique of high intensity high-hardness alloy and roll forming equipment
A high-hardness, high-strength technology, applied in the integrated rolling and forging process of high-strength, refractory alloy materials and its rolling and forging equipment, high hardness field, can solve the large difference in homogeneity between the surface layer and the core, processing difficulties, Difficulties and other problems, to achieve the effect of simple, practical and efficient process flow, simple and compact equipment structure, and good internal crystallization structure
- Summary
- Abstract
- Description
- Claims
- Application Information
AI Technical Summary
Problems solved by technology
Method used
Image
Examples
Embodiment Construction
[0024] Below in conjunction with accompanying drawing, specific embodiment of the present invention is described in further detail:
[0025] As shown in Figure 1 and Figure 2, the driving device 4 of the active frame can be connected with the main frame 2 through a connecting mechanism such as a connecting rod, and the driving device 4 of the active frame pulls the driving frame 2 through a connecting mechanism such as a connecting rod at a rate of 30 to 60 times / min. The frequency is done horizontal reciprocating motion, and the eccentric roll 5 that is installed on the driving frame 2 is except doing horizontal reciprocating motion with main frame 2, also does left and right swing rotation. When the main frame 2 is located on the leftmost side (feed side), the eccentric roll pull rod device 8 will push the eccentric roll 5 away from the surface of the billet 9, and as the main frame 2 moves to the right (feed side), the eccentric roll 5 will Pulled by the roller pull rod dev...
PUM
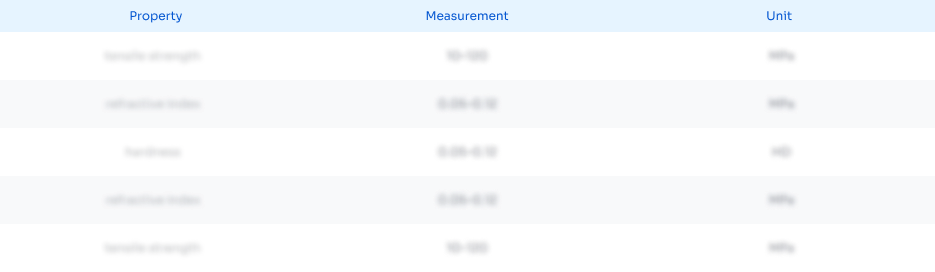
Abstract
Description
Claims
Application Information

- R&D
- Intellectual Property
- Life Sciences
- Materials
- Tech Scout
- Unparalleled Data Quality
- Higher Quality Content
- 60% Fewer Hallucinations
Browse by: Latest US Patents, China's latest patents, Technical Efficacy Thesaurus, Application Domain, Technology Topic, Popular Technical Reports.
© 2025 PatSnap. All rights reserved.Legal|Privacy policy|Modern Slavery Act Transparency Statement|Sitemap|About US| Contact US: help@patsnap.com