Method for preparing amorphous alloy needle
An alloy needle and amorphous technology, which is applied in the field of preparation of alloy needles, achieves the effects of good biocompatibility, convenient operation, and excellent comprehensive performance
- Summary
- Abstract
- Description
- Claims
- Application Information
AI Technical Summary
Problems solved by technology
Method used
Image
Examples
specific Embodiment approach 1
[0011] Specific Embodiment 1: In this embodiment, the preparation of amorphous alloy needles is carried out according to the following steps: the master alloy is placed in an inert atmosphere with a pressure of 0.02-0.07 MPa for arc melting, and then the master alloy melt is formed by copper mold suction casting. The amorphous alloy needle is obtained; the master alloy is Zr 51 Cu 24.22 Ni 14.06 Al 10.72 , Fe 36-45 co 2-5 Cr 15 Mo 14 C 15 B 6 Y 1-5 、Cu 44-54 Ti 30-38 Zr 6-12 Ni 6-9 、Ti 40 Zr 25 Ni 3 Cu 12 be 20 、Ti 40-45 Zr 2-5 f 4-6 Cu 37-43 Ni 7 Si 1 sn 0-9 or Ni 40-42 Ti 22-27 Zr 20-26 Al 7-9 Cu 5 Si 2-6 .
[0012] In conjunction with Fig. 1 and Fig. 2, the copper mold suction casting method of the present embodiment is illustrated: the master alloy melt is sucked in the metal copper mold cavity 2 of the amorphous alloy needle (the cavity 2 is composed of the left lobe mold 1 and the right lobe mold of the metal copper mold). The valve mold 3...
specific Embodiment approach 2
[0017] Embodiment 2: The difference between this embodiment and Embodiment 1 is that the master alloy is arc-melted in an inert atmosphere with a pressure of 0.05 MPa. Others are the same as in the first embodiment.
specific Embodiment approach 3
[0018] Embodiment 3: The difference between this embodiment and Embodiment 1 is that: vacuumize first and then fill with inert gas to form an inert atmosphere. Others are the same as in the first embodiment.
PUM
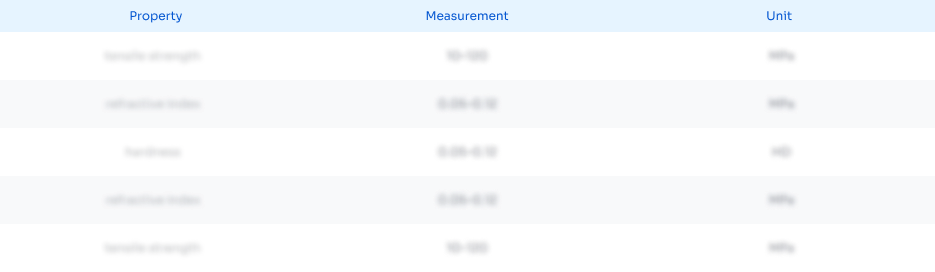
Abstract
Description
Claims
Application Information

- R&D Engineer
- R&D Manager
- IP Professional
- Industry Leading Data Capabilities
- Powerful AI technology
- Patent DNA Extraction
Browse by: Latest US Patents, China's latest patents, Technical Efficacy Thesaurus, Application Domain, Technology Topic, Popular Technical Reports.
© 2024 PatSnap. All rights reserved.Legal|Privacy policy|Modern Slavery Act Transparency Statement|Sitemap|About US| Contact US: help@patsnap.com