Method for preparing cellulose and carboxymethyl cethylose by wood fibre material
A technology of carboxymethyl cellulose and lignocellulosic materials, applied in the field of preparing high-purity carboxymethyl cellulose, can solve the problems of consuming energy and chemical raw materials, discharging waste liquid containing sulfite, waste of resources and the environment, and achieving Easy handling, low production cost, and time-saving effect
- Summary
- Abstract
- Description
- Claims
- Application Information
AI Technical Summary
Problems solved by technology
Method used
Image
Examples
Embodiment 1
[0040] Crush 20 grams of bagasse or wheat straw into pieces and granules to 0.1-2 mm with a pulverizer, add 200 ml of distilled water to soak to make a suspension, adjust the pH of the solution to 11-12 with 1N sodium hydroxide, add 30% Hydrogen peroxide, 750w microwave irradiation for 10 minutes. Add 1N hydrochloric acid to neutralize and adjust the pH to 6.5-7.5. After filtration, the remaining cellulose filter residue is washed repeatedly with 70% ethanol, and finally placed in a constant temperature drying oven to dry to constant weight. The resulting cellulose is identified by infrared spectroscopy. , quantitatively measure cellulose and lignin according to the literature method (Chen Hongzhang, Cellulose Biotechnology, Chemical Industry Press, first edition in July 2005, 231-237), and the cellulose content reaches 99%.
Embodiment 2
[0042] In a 250ml beaker, add 10g of the cellulose prepared in Example 1, 140ml of 95% ethanol, dropwise add 20g of 20% sodium hydroxide solution, and add 30% hydrogen peroxide, stir and basify at room temperature for 50min, then add 9g of a Ethanol solution of chloroacetic acid (1:1) was reacted under microwave irradiation for 10 min. After the reaction, the product was neutralized with 1N hydrochloric acid, the pH value was adjusted to 6.5-7.5, filtered, washed twice with 75%-85% ethanol, and washed once with 95% ethanol. Dry at 60°C and pulverize to obtain carboxymethyl cellulose product in the form of white powder.
Embodiment 3
[0044] Crush 20 grams of bagasse into pieces and particles to 0.1-2 mm with a pulverizer, add 200 ml of distilled water to soak to make a suspension, adjust the pH of the solution to 11-12 with 1N sodium hydroxide, add 5 ml of 30% hydrogen peroxide And 9g9g ethanol solution of chloroacetic acid (1:1), 750w microwave radiation for 10 minutes. After the reaction, the product was neutralized with 1N hydrochloric acid, adjusted to pH 6.5-7.5, filtered, washed twice with 75%-85% ethanol, and washed once with 95% ethanol. Dry at 60°C and crush to obtain white powdery carboxymethyl cellulose product directly.
PUM
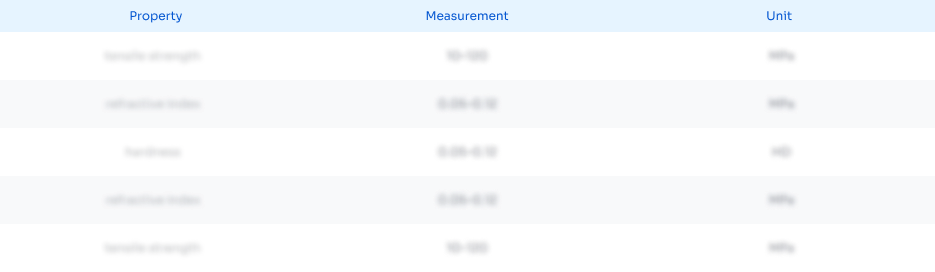
Abstract
Description
Claims
Application Information

- R&D Engineer
- R&D Manager
- IP Professional
- Industry Leading Data Capabilities
- Powerful AI technology
- Patent DNA Extraction
Browse by: Latest US Patents, China's latest patents, Technical Efficacy Thesaurus, Application Domain, Technology Topic, Popular Technical Reports.
© 2024 PatSnap. All rights reserved.Legal|Privacy policy|Modern Slavery Act Transparency Statement|Sitemap|About US| Contact US: help@patsnap.com