Method for preparing tin content step-up PVD bushing in antifriction layer
A bearing and content technology, applied in the field of preparing PVD bearing pads with tin content in the antifriction layer, can solve the problems of stickiness, unreasonable content and distribution of tin components in the sliding layer, affecting the performance of PVD bearing pads, etc., so as to improve the adhesion Effect of strength, good anti-stick properties or run-in properties
- Summary
- Abstract
- Description
- Claims
- Application Information
AI Technical Summary
Problems solved by technology
Method used
Image
Examples
Embodiment 1
[0017] (1) Target preparation
[0018] The nickel target adopts a nickel target with a purity of 99.99%; the aluminum alloy target is configured with pure tin, pure copper and pure aluminum in a ratio of 16%: 0.3%: 83.7% by weight, and is first smelted into blocks in an electric arc melting furnace Shaped alloy, then extruded, cooled to room temperature with the furnace, and processed into a sputtering target that meets the requirements of the sputtering instrument.
[0019] (2) Bearing base pretreatment
[0020] First, polish the bearing bush, then put it into the treatment tank, remove the oxide layer and oil stain through chemical degreasing, pickling, electrolytic degreasing and ultrasonic cleaning, and then put it into the oven for drying. on the fixture in the shooting bay.
[0021] (3) PVD bearing bush prepared by sputtering
[0022] ① Sputtering nickel gate layer 4
[0023] The nickel gate layer is sputtered with conventional process steps and process parameters. ...
Embodiment 2
[0033] (1) Target preparation
[0034]The nickel target material is a nickel target with a purity of 99.99%. The aluminum alloy target material is configured with pure tin, pure copper and pure aluminum in a ratio of 20%: 1.6%: 78.4% by weight. Other steps are the same as in Example 1.
[0035] (2) Bearing base pretreatment
[0036] This step is the same as in Example 1.
[0037] (3) PVD bearing bush prepared by sputtering
[0038] ① Sputtering the first diffusion layer 3
[0039] Before the nickel grid layer is sputtered in Example 1, the sputtering diffusion layer step is added to improve the adhesion strength between the nickel grid layer and the substrate. The substrate lining layer 1 where the bearing bush substrate participates in mutual sputtering is CuPbSn, and the substrate temperature is 50°C. The air pressure is 0.4Pa, the negative bias of the PVD bearing substrate is -1700V; the current of the PVD bearing substrate is 2A; the negative bias of the nickel target i...
Embodiment 3
[0053] (1) Target preparation
[0054] The nickel target material is a nickel target with a purity of 99.99%; the aluminum alloy target material is configured with pure tin, pure copper and pure aluminum in a ratio of 25%:3%:72% by weight, and other steps are the same as in Example 1.
[0055] (2) Bearing base pretreatment
[0056] This step is the same as in Example 1.
[0057] (3) PVD bearing bush prepared by sputtering
[0058] ① Sputtering the first diffusion layer 3
[0059] The process and equipment are the same as in Example 1, except that the process conditions of the magnetron sputtering first diffusion layer 3 are as follows: the substrate temperature is 98°C, the sputtering pressure is 1Pa, and the negative bias voltage of the PVD bearing substrate is -300V; The PVD bearing substrate current is 0.5A; the negative bias voltage of the nickel target is -620V; the nickel target current is 1A; the treatment time: 40 minutes; the weight percentage of each component of ...
PUM
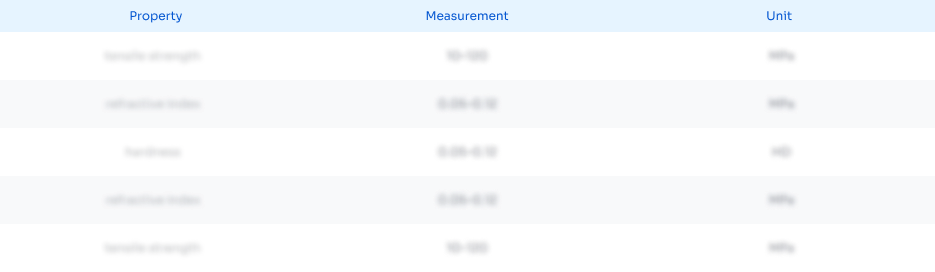
Abstract
Description
Claims
Application Information

- R&D Engineer
- R&D Manager
- IP Professional
- Industry Leading Data Capabilities
- Powerful AI technology
- Patent DNA Extraction
Browse by: Latest US Patents, China's latest patents, Technical Efficacy Thesaurus, Application Domain, Technology Topic, Popular Technical Reports.
© 2024 PatSnap. All rights reserved.Legal|Privacy policy|Modern Slavery Act Transparency Statement|Sitemap|About US| Contact US: help@patsnap.com