Non-poaching-water common hot-dip galvanizing technique
A technology of hot-dip galvanizing without rinsing, applied in hot-dip galvanizing process, metal material coating process, coating, etc., which can solve the problems of water consumption and treatment cost increase, so as to save water resources and increase galvanizing Great effect on cost, social and economic benefits
- Summary
- Abstract
- Description
- Claims
- Application Information
AI Technical Summary
Problems solved by technology
Method used
Image
Examples
Embodiment 1
[0032] Embodiment 1: the ordinary hot-dip galvanizing process without rinsing water of this example is as shown in Figure 1, and the steps are as follows:
[0033] a. Degreasing: immerse the workpiece to be galvanized in the degreasing solution to remove all kinds of grease pollution on the surface of the workpiece to be galvanized. The degreasing solution is an aqueous solution of non-phosphorus degreasing agent, which contains 2% of non-phosphorus degreasing agent, the temperature is controlled at 40°C, the degreasing and immersion time is determined according to the degree of oil pollution, and it is 10 minutes. The qualified standard for degreasing treatment is that there is no oil on the surface of the plating Impurity attachment;
[0034] b. Pickling: immerse the workpiece to be galvanized without oil pollution in the pickling solution to remove the iron oxide on the surface of the plated piece, that is, Fe 2 o 3 , Fe 3 o 4 , FeO, to ensure the smooth progress of the...
Embodiment 2
[0040] Embodiment 2: the ordinary hot-dip galvanizing process without rinsing water of this example is as shown in Figure 1, and the steps are as follows:
[0041] a. Degreasing: immerse the workpiece to be galvanized in the degreasing solution to remove all kinds of grease pollution on the surface of the workpiece to be galvanized. The degreasing liquid is an aqueous solution of non-phosphorus degreasing agent, which contains 1% of non-phosphorus degreasing agent. The temperature is controlled at 45°C. The degreasing and immersion time is determined according to the degree of oil pollution, which is 15 minutes. The qualified standard for degreasing treatment is that there is no oil on the surface of the plating Impurity attachment;
[0042] b. Pickling: immerse the workpiece to be galvanized without oil pollution in the pickling solution to remove the iron oxide on the surface of the plated piece, that is, Fe 2 o 3 , Fe 3 o 4 , FeO, to ensure the smooth progress of the zi...
Embodiment 3
[0048] Embodiment 3: the ordinary hot-dip galvanizing process without rinsing water of this example is as shown in Figure 1, and the steps are as follows:
[0049] a. Degreasing: immerse the workpiece to be galvanized in the degreasing solution to remove all kinds of grease pollution on the surface of the workpiece to be galvanized. The degreasing solution is an aqueous solution of non-phosphorus degreasing agent, which contains 3% of non-phosphorus degreasing agent, the temperature is controlled at 50°C, the degreasing and immersion time is determined according to the degree of oil pollution, and it is 11 minutes. The qualified standard for degreasing treatment is that there is no oil on the surface of the plating Impurity attachment;
[0050] b. Pickling: immerse the workpiece to be galvanized without oil pollution in the pickling solution to remove the iron oxide on the surface of the plated piece, that is, Fe 2 o 3 , Fe 3 o 4 , FeO, to ensure the smooth progress of the...
PUM
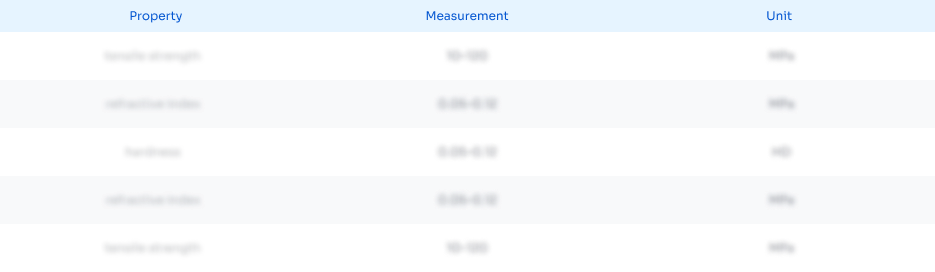
Abstract
Description
Claims
Application Information

- R&D
- Intellectual Property
- Life Sciences
- Materials
- Tech Scout
- Unparalleled Data Quality
- Higher Quality Content
- 60% Fewer Hallucinations
Browse by: Latest US Patents, China's latest patents, Technical Efficacy Thesaurus, Application Domain, Technology Topic, Popular Technical Reports.
© 2025 PatSnap. All rights reserved.Legal|Privacy policy|Modern Slavery Act Transparency Statement|Sitemap|About US| Contact US: help@patsnap.com