Medicine gradient zero level implantation controlled-release drug administration device and preparation thereof
A drug delivery device and drug technology, applied in the direction of medical formula, drug delivery, medical preparations of non-active ingredients, etc., can solve the problems of insufficient research and development, and achieve simple preparation process, good reproducibility, and high degree of automation Effect
- Summary
- Abstract
- Description
- Claims
- Application Information
AI Technical Summary
Problems solved by technology
Method used
Image
Examples
Embodiment 1
[0034] Embodiment 1: the deployment of layer powder and binder
[0035] Pass polylactic acid through a 200-mesh sieve, and take powder with a particle size of less than 74 μm for the top and bottom layers; weigh 2 grams of polylactic acid powder, dissolve it in 50 mL of acetone, and prepare a polylactic acid containing 4% (w / v) The top and bottom powder forming binders.
[0036] The raw material composition and content (by weight percentage) of intermediate mixing powder are as follows:
[0037] Polylactic acid 100 parts
[0038] Colloidal silicon dioxide 2 parts
[0039] Macrogol 6000 20 parts
[0040] Weigh 13 grams of the drug chloramphenicol and dissolve in 100 mL of acetone to prepare an intermediate mixed powder forming binder.
Embodiment 2
[0041] Example 2: Determining 3D printing forming parameters
[0042] Top and bottom surface spray forming parameters:
[0043] Layer interval time 3min
[0044] Powder layer thickness 200μm
[0045] Spraying rate [spraying drop volume (droplet quantity × droplet size) × spraying frequency] 0.4nL × 12kz
[0046] Spray times 3 times
[0047] Parameters of intermediate medicated mixed powder spraying:
[0048] Layer interval time 5min
[0049] Powder layer thickness 200μm
[0050] Spraying rate [spraying drop volume (droplet quantity × droplet size) × spraying frequency] 0.4nL × 12kz
[0051] Spraying times 5 times
Embodiment 3
[0052] Example 3: Preparation of Drug Gradient Drug Delivery Device
[0053] The operation and preparation are directly controlled by the computer terminal output instructions. First lay a layer of polylactic acid powder with a thickness of 200 μm, spray 4% polylactic acid acetone solution three times as a binder to form the bottom surface of the drug delivery device, and then the piston rod drives the powder bed of the workbench to descend as a whole to prepare a new layer of polylactic acid powder. pink.
[0054] The middle layer is a mixed powder of polylactic acid and other auxiliary materials, the thickness of the layer is 200 μm, and the acetone solution containing 13% chloramphenicol is used as a binder. times, repeat 30 layers.
[0055] Subsequently, another layer of polylactic acid powder with a thickness of 200 μm was spread, and 4% (w / v) polylactic acid acetone solution was sprayed three times as a binder to form the top surface of the drug delivery device. Final...
PUM
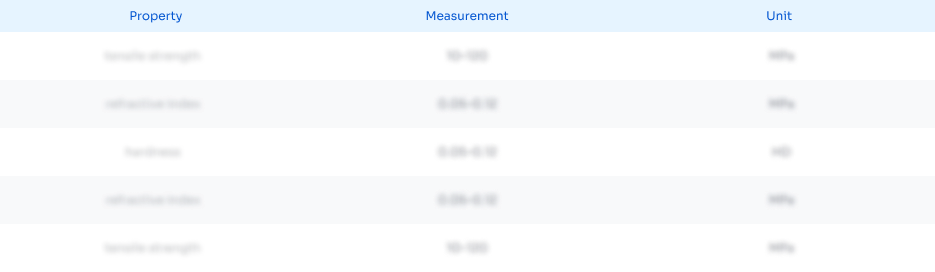
Abstract
Description
Claims
Application Information

- R&D
- Intellectual Property
- Life Sciences
- Materials
- Tech Scout
- Unparalleled Data Quality
- Higher Quality Content
- 60% Fewer Hallucinations
Browse by: Latest US Patents, China's latest patents, Technical Efficacy Thesaurus, Application Domain, Technology Topic, Popular Technical Reports.
© 2025 PatSnap. All rights reserved.Legal|Privacy policy|Modern Slavery Act Transparency Statement|Sitemap|About US| Contact US: help@patsnap.com