Method for extracting vanadic anhydride from stone coal vanadium ore
A technology for vanadium pentoxide and stone coal vanadium, which is applied in the field of vanadium pentoxide extraction, can solve the problems of low leaching rate, workshop dust pollution, large sulfuric acid consumption, etc., and achieves improved leaching recovery rate and high degree of mechanization. , the effect of reducing workload
- Summary
- Abstract
- Description
- Claims
- Application Information
AI Technical Summary
Problems solved by technology
Method used
Examples
Embodiment 1
[0045] 1. Mineral dressing: first select stone coal vanadium ore (fixed carbon content 5-10%), carry out coarse crushing and fine crushing, and control stone coal vanadium ore particle size 8-12cm to account for 25-30%;
[0046] 2. Roasting: Put the crushed stone coal vanadium ore into a rotary kiln, rotary kiln or tunnel kiln for roasting, control the furnace temperature to 750°C, and the output temperature of the obtained roasted material is 750°C;
[0047] 3. At a temperature of 750°C, enter the heat preservation silo for static heat preservation for 24 hours;
[0048] 4. Leaching. The roasted roasted material has an average grade of 0.722% and a leaching rate of 64.23%. It is sprayed with sulfuric acid with a mass percentage concentration of 5-6%. The acid consumption is 86kg / T, and the obtained leaching solution is used Shuangfei powder adjusts the pH value to 2.5, flows through D201 resin for adsorption;
[0049] 5. Alkali adjustment: in the early stage of leaching, the...
Embodiment 2
[0064] Control furnace temperature 850 ℃, the discharge temperature of roasting material 850 ℃, the holding time of holding bin is 48 hours, and its transfer leaching rate is 86.34%, all the other are the same as embodiment 1.
Embodiment 3
[0066] Control the furnace temperature to 900°C, the discharge temperature of the roasted material to 900°C, the holding time of the heat preservation bin to be 72 hours, and the leaching rate to be 94.42%. All the other are the same as in Example 1.
PUM
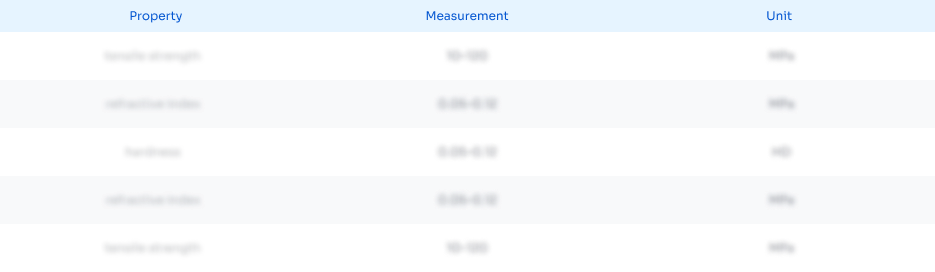
Abstract
Description
Claims
Application Information

- Generate Ideas
- Intellectual Property
- Life Sciences
- Materials
- Tech Scout
- Unparalleled Data Quality
- Higher Quality Content
- 60% Fewer Hallucinations
Browse by: Latest US Patents, China's latest patents, Technical Efficacy Thesaurus, Application Domain, Technology Topic, Popular Technical Reports.
© 2025 PatSnap. All rights reserved.Legal|Privacy policy|Modern Slavery Act Transparency Statement|Sitemap|About US| Contact US: help@patsnap.com