Kapok flocculus and production method thereof
A production method and technology of wadding, applied in textiles, papermaking, non-woven fabrics, etc., can solve the problems of floc bulkiness, compression resilience difficult to achieve, bulkiness, compression resilience reduction, etc., to achieve good mite repelling and Bacteriostatic effect, improved strength and compression elasticity, and high heat retention effect
- Summary
- Abstract
- Description
- Claims
- Application Information
AI Technical Summary
Problems solved by technology
Method used
Examples
Embodiment 1
[0047] Used flakes Quantitative 265g / m 2
[0048] The components and percentages by weight of selected fiber raw materials are: 60% of kapok fiber; 8% of cellulose fiber; 25% of polyester porous fiber; 7% of polyester three-dimensional crimped fiber, and operate according to the following technological process respectively: 1, open and clean cotton; 2. Opening and mixing cotton; 3. Vibrating cotton box: the quantitative output cotton layer is 950g / m 2 ; 4. Carding: among them, the weight of the upper doffer peeling cotton net is 16-17g / m 2 , Quantitative ration of cotton net under doffer stripping 14~15g / m 2 5. Laying net; 6. Messy drafting and powdering: wherein the drafting ratio is 1.25:1, and the powdering rate is 9%; 7. Hot melting; 8. Ironing; 9. Cooling.
Embodiment 2
[0050] Pillow core and mattress flakes Quantitative 135g / m 2
[0051] The components and percentages by weight of selected fiber raw materials are: 40% of kapok fiber; 10% of cellulose fiber; 32% of polyester porous fiber; 18% of polyester three-dimensional crimped fiber, and operate according to the following technological process respectively: 1, open and clean cotton; 2. Opening and blending of cotton; 3. Vibrating cotton box: the quantitative output of cotton layer is 700g / m 2 ; 4. Carding: among them, the weight of the upper doffer peeling cotton net is 13-14g / m 2, Quantitative weight of the cotton net in the lower doffer stripping cotton is 12~13g / m 2 ; 5. Laying net; 6. Messy drafting and powdering: wherein the drafting ratio is 1.5:1, and the powdering rate is 13%; 7. Hot melting; 8. Ironing; 9. Cooling.
Embodiment 3
[0053] Quantitative flakes for clothing 125g / m 2
[0054] The components and percentages by weight of selected fiber raw materials are: 68% of kapok fiber; 12% of cellulose fiber; 13% of polyester porous fiber; 7% of polyester three-dimensional crimped fiber, and operate according to the following technological process respectively: 1, open and clean cotton; 2. Opening and blending of cotton; 3. Vibrating cotton box: the quantitative output of cotton layer is 700g / m 2 ; 4. Carding: among them, the weight of the upper doffer peeling cotton net is 13-14g / m 2 , Quantitative weight of the cotton net in the lower doffer stripping cotton is 12~13g / m 2 ;5. Laying; 6. Messy drafting and powdering: wherein the drafting ratio is 1.5:1, and the powdering rate is 10%; 7. Hot melting; 8. Ironing; 9. Cooling.
PUM
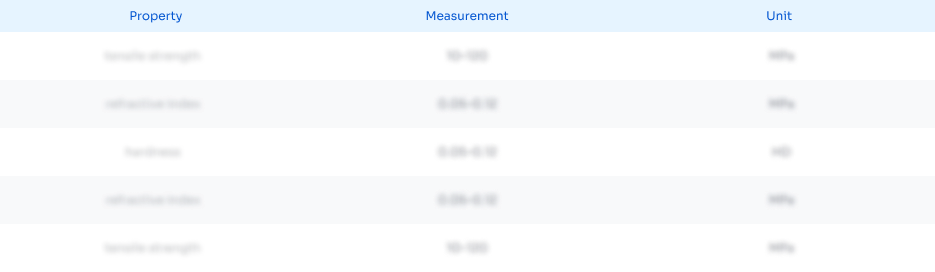
Abstract
Description
Claims
Application Information

- R&D
- Intellectual Property
- Life Sciences
- Materials
- Tech Scout
- Unparalleled Data Quality
- Higher Quality Content
- 60% Fewer Hallucinations
Browse by: Latest US Patents, China's latest patents, Technical Efficacy Thesaurus, Application Domain, Technology Topic, Popular Technical Reports.
© 2025 PatSnap. All rights reserved.Legal|Privacy policy|Modern Slavery Act Transparency Statement|Sitemap|About US| Contact US: help@patsnap.com