Method for recycling acetic acid in dilute acetic acid
A technology of dilute acetic acid and acetic acid, which can be used in solvent extraction of liquid solutions, separation/purification of carboxylic acid compounds, organic chemistry, etc., and can solve problems such as low separation efficiency
- Summary
- Abstract
- Description
- Claims
- Application Information
AI Technical Summary
Problems solved by technology
Method used
Image
Examples
Embodiment 1
[0021] The extraction tower is filled with 3 mm × mm θ ring wire mesh packing, with an effective height of 1.2 meters, which is equivalent to 11 theoretical plates. The weight percentage of acetic acid in the dilute acetic acid solution is 6.8%, the percentage of water is 93.2%, and the extraction agent Percentage by weight: mixed amine (tributylamine and tripentylamine account for 35% and 65% by weight respectively, hereinafter the same) is 32.5%, n-octanol is 48.7%, kerosene fraction above 160°C is 18.8% , the dilute acetic acid solution and the extractant both enter the top and bottom of the extraction tower at a flow rate of 0.70 kg / h, the extraction temperature is 35°C, the air compressor pressure is 150kPa, and the pulse frequency of the solenoid valve is 0.05 seconds-1. After the operation is stable, the extraction phase And the temperature of raffinate phase is 40 ℃ and 37 ℃ respectively, and analysis obtains the composition of extract phase and raffinate phase and sees...
Embodiment 2
[0025] Keep other conditions of the extraction tower as in Example 1, change the composition of the extractant, the mixed amine weight content is 21.2%, the n-octanol weight content is 42.6%, the kerosene weight content is 36.2%, the analysis obtains the extraction phase and the raffinate phase The composition is shown in the table below. After being separated by the whole technological process, the recovery rate of acetic acid is 92%.
[0026] Extraction tower extraction result
[0027]
Embodiment 3
[0029] Keep other conditions of the extraction tower as in Example 1, change the extraction temperature to 60° C., and analyze the composition of the extract phase and raffinate phase as shown in the table below. After being separated by the whole technological process, the recovery rate of acetic acid is 85%.
[0030] Extraction tower extraction result
[0031]
PUM
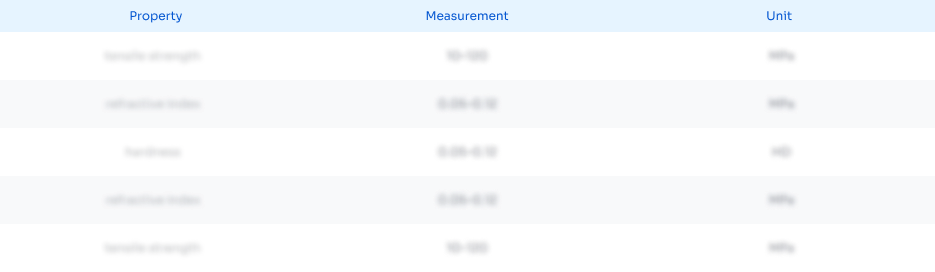
Abstract
Description
Claims
Application Information

- R&D
- Intellectual Property
- Life Sciences
- Materials
- Tech Scout
- Unparalleled Data Quality
- Higher Quality Content
- 60% Fewer Hallucinations
Browse by: Latest US Patents, China's latest patents, Technical Efficacy Thesaurus, Application Domain, Technology Topic, Popular Technical Reports.
© 2025 PatSnap. All rights reserved.Legal|Privacy policy|Modern Slavery Act Transparency Statement|Sitemap|About US| Contact US: help@patsnap.com