Process for producing self-cleaning absorbent charcoal material for carbon carving technique
A self-cleaning and activated carbon technology is applied in the field of preparation of self-cleaning activated carbon materials, which can solve the problems of complex technology of activated carbon materials, and achieve the effects of low cost, permanent service life, and beautifying the decorative environment.
- Summary
- Abstract
- Description
- Claims
- Application Information
AI Technical Summary
Problems solved by technology
Method used
Examples
Embodiment 1
[0016] Example 1: First, 500g of powdered activated carbon of 100 mesh, 150g of mesophase pitch of 100 mesh, and 50g of tetra-n-butyl titanate were mixed on a high-speed mixer for 15 minutes to prepare pre-mixed powder; then the pre-mixed powder was put into the ball mill Add 200ml of ethanol and grind and react for 15 hours; the ground mixture is aged and dried at room temperature for 50 hours and crushed to 60 mesh; the above powdery mixture is added to the mold, preformed by cold pressing at 5MPa, and then heated When it reaches 280°C, start pressurization and molding, the pressure is 50MPa, keep it at this pressure for 30 minutes, then stop heating and natural cooling; then the obtained block material is carbonized in a high temperature furnace, nitrogen is selected as the protective gas, and the carbonization heating rate is 1°C / min, the carbonization temperature is 900°C; when the temperature reaches 900°C, the vacuum reaches 2Pa, and the pressure is kept for 2 hours; then...
Embodiment 2
[0017] Example 2: First, 1000 g of powdered activated carbon with 200 mesh, 200 g of mesophase pitch with 100 mesh, and 100 g of tetra-n-butyl titanate were mixed on a high-speed mixer for 10 minutes to prepare pre-mixed powder; then the pre-mixed powder was put into the ball mill Add 300ml of ethanol and grind and react for 5 hours; the ground mixture is aged and dried at room temperature for 100 hours and crushed to 100 mesh; the above powdery mixture is added to the mold, preformed by cold pressing at 3MPa, and then heated When it reaches 300°C, start pressurization and molding, the pressure is 100MPa, keep it for 30 minutes at this pressure, then stop heating and cool naturally; place the obtained block material in a high-temperature furnace for carbonization, select nitrogen as the protective gas, and the carbonization heating rate is 0.5 ℃ / min, the carbonization temperature is 800℃; when the temperature reaches 800℃, vacuumize to 1Pa, keep the pressure for 1 hour; then dec...
Embodiment 3
[0018] Example 3: First, 2,000 g of 100 mesh powdered activated carbon, 400 g of 100 mesh mesophase pitch, and 200 g of tetra-n-butyl titanate were mixed on a high-speed mixer for 15 minutes to prepare pre-mixed powder; then the pre-mixed powder was put into the ball mill Add 600ml of ethanol and grind and react for 20 hours; the ground mixture is aged and dried at room temperature for 100 hours and crushed to 60 mesh; the above powdery mixture is added to the mold, preformed by cold pressing at 5MPa, and then heated When it reaches 300°C, start pressurization and molding, the pressure is 100MPa, keep it for 30 minutes at this pressure, then stop heating and cool naturally; place the obtained block material in a high-temperature furnace for carbonization, select nitrogen as the protective gas, and the carbonization heating rate is 0.5 ℃ / min, the carbonization temperature is 850℃; when the temperature reaches 850℃, vacuumize to 1Pa, keep the pressure for 1 hour; then decrease the...
PUM
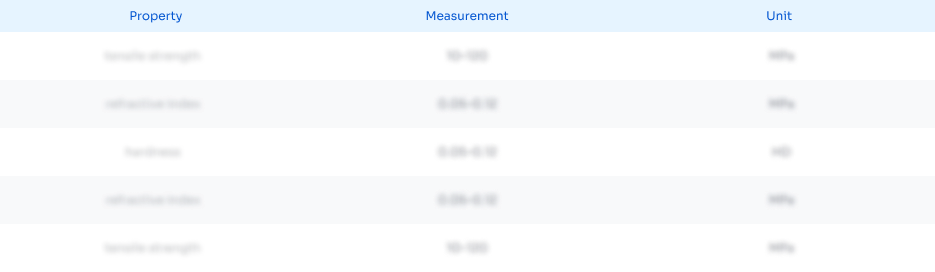
Abstract
Description
Claims
Application Information

- R&D
- Intellectual Property
- Life Sciences
- Materials
- Tech Scout
- Unparalleled Data Quality
- Higher Quality Content
- 60% Fewer Hallucinations
Browse by: Latest US Patents, China's latest patents, Technical Efficacy Thesaurus, Application Domain, Technology Topic, Popular Technical Reports.
© 2025 PatSnap. All rights reserved.Legal|Privacy policy|Modern Slavery Act Transparency Statement|Sitemap|About US| Contact US: help@patsnap.com