Method for producing light high strength sintered brick using with city sludge and wet-discharged flyash
A technology for wet discharge of fly ash and urban sludge, which is applied to chemical instruments and methods, applications, household appliances, etc., can solve the problems of large capacity and thermal insulation performance that cannot meet building energy conservation, and achieve low production costs and benefit Effects of Building Energy Conservation and Environmental Protection
- Summary
- Abstract
- Description
- Claims
- Application Information
AI Technical Summary
Problems solved by technology
Method used
Examples
Embodiment 1
[0011] Embodiment 1: The raw material composition and the weight percent of the lightweight high-strength sintered brick of this embodiment are: municipal sludge (moisture content 75%) 35%, wet discharge fly ash 60%, perlite powder 3%, sawdust 2% %.
[0012] The preparation process of the present embodiment comprises the following steps:
[0013] (1) Mixing of raw materials: Stir and mix urban sludge, wet-discharged fly ash, perlite powder, sawdust, etc. in proportion, and control the moisture content of the mixture at about 18.
[0014] (2) Forming: Input the mixed materials into the hydraulic brick making machine to form solid bricks.
[0015] (3) Drying: reduce the brick content to below 6% by natural drying.
[0016] (4) Roasting: Send the dried bricks into the kiln for roasting, the maximum firing temperature is 1100°C, and the maximum temperature holding time is 4 hours, that is, the standard solid brick product is fired.
Embodiment 2
[0017] Embodiment 2: The raw material composition and the weight percent of the lightweight high-strength sintered brick of this embodiment are: municipal sludge (moisture content 75%) 40%, wet discharge fly ash 55%, bentonite 4%, rice husk 1% .
[0018] The preparation process of the present embodiment comprises the following steps:
[0019] (1) Mixing of raw materials: Stir and mix urban sludge, wet-discharged fly ash, perlite powder, sawdust, etc. in proportion, and control the moisture content of the mixture at about 18.
[0020] (2) Forming: Input the mixed material into the hydraulic brick making machine to form porous bricks.
[0021] (3) Drying: reduce the brick content to below 6% by natural drying.
[0022] (4) Roasting: send the dried bricks into the kiln for firing, the maximum firing temperature is 1080°C, and the maximum temperature holding time is 4 hours, that is, the finished porous brick is fired.
Embodiment 3
[0023] Embodiment 3: The raw material composition and the weight percent of the lightweight high-strength sintered brick of this embodiment are: municipal sludge (moisture content 75%) 30%, wet discharge fly ash 65%, diatomaceous earth 3%, polystyrene Granules 2%.
[0024] The preparation process is the same as in Example 1.
PUM
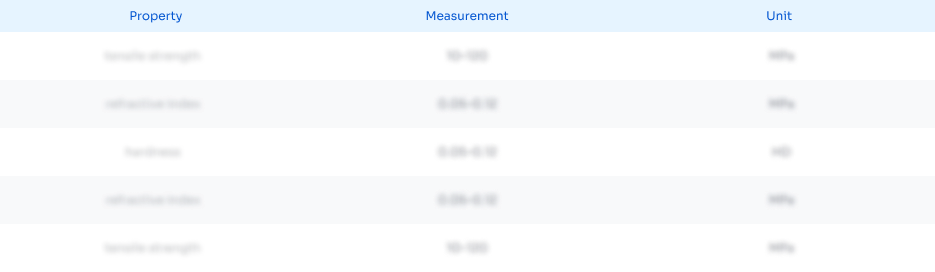
Abstract
Description
Claims
Application Information

- R&D Engineer
- R&D Manager
- IP Professional
- Industry Leading Data Capabilities
- Powerful AI technology
- Patent DNA Extraction
Browse by: Latest US Patents, China's latest patents, Technical Efficacy Thesaurus, Application Domain, Technology Topic, Popular Technical Reports.
© 2024 PatSnap. All rights reserved.Legal|Privacy policy|Modern Slavery Act Transparency Statement|Sitemap|About US| Contact US: help@patsnap.com