Casting blank heating method for controlling surface to generate ferric oxide structure
A technology of iron oxide scale and surface control, applied in rolling mill control devices, workpiece surface treatment equipment, heat treatment furnaces, etc., can solve the problems of uneven surface of rolls, pitting on the surface of rails, etc., so as to reduce the grinding time of rolls and improve the operation rate of steel rolling. Effect
- Summary
- Abstract
- Description
- Claims
- Application Information
AI Technical Summary
Problems solved by technology
Method used
Image
Examples
Embodiment 1
[0025] The cross-sectional size of the rail blanks for manufacturing is 280×380mm, and they are loaded into the furnace in groups by the steel charging machine of the heating furnace. There is a gap of 170mm between the two blanks, and there are 26 blanks in each group. Distance, through the progressive beam of the heating furnace, the distance of stepping 550mm at a time is the cycle. According to the rolling rhythm, the billet is sent from the entrance of the heating furnace to the preheating section for preheating. The furnace temperature in the preheating section is 600°C; after preheating The billet enters the first heating section through the progressive beam for heating. The furnace temperature of the first heating section is 1150°C, and the ratio of air and gas in the heating gas is 1:2.0; the billet heated through the first heating section enters the second Heating in the heating section, the furnace temperature of the second heating section is 1280°C, the ratio of air...
Embodiment 2
[0027] The cross-sectional size of the rail blanks for manufacturing is 280×380mm, and they are loaded into the furnace in groups by the steel charging machine of the heating furnace. There is a gap of 120mm between the two blanks. Distance, through the progressive beam of the heating furnace, the distance of stepping 500mm at a time is the period. According to the rolling rhythm, the billet is sent from the entrance of the heating furnace to the preheating section for preheating. The furnace temperature in the preheating section is 570°C. When the billet passes through When the advancing beam is sent to the end of the preheating section, the heating furnace waits for rolling for 30 minutes. At this time, the furnace temperature of the first heating section should be controlled at 1000°C, and the ratio of air and gas in the heating gas should be 1:1.9; the furnace temperature of the second heating section should be 1240°C, and the ratio of air and gas in the heating gas The ra...
Embodiment 3
[0029] The cross-sectional size of the rail blanks for manufacturing is 450×360mm, and they are loaded into the furnace in groups by the steel charging machine of the heating furnace. There is a gap of 170mm between the two blanks, and there are 23 blanks in each group. Distance, through the progressive beam of the heating furnace, the distance of 620mm is taken as a cycle. According to the rolling rhythm, the billet is sent from the entrance of the heating furnace to the preheating section for preheating. The furnace temperature in the preheating section is 580°C; after preheating The billet enters the first heating section through the progressive beam for heating. At this time, the heating furnace is to be rolled for 60 minutes. The furnace temperature of the first heating section should be controlled at 1000°C, and the ratio of air and gas in the heating gas is 1:1.9; the second The furnace temperature in the heating section is 1220°C, and the ratio of air and gas in the hea...
PUM
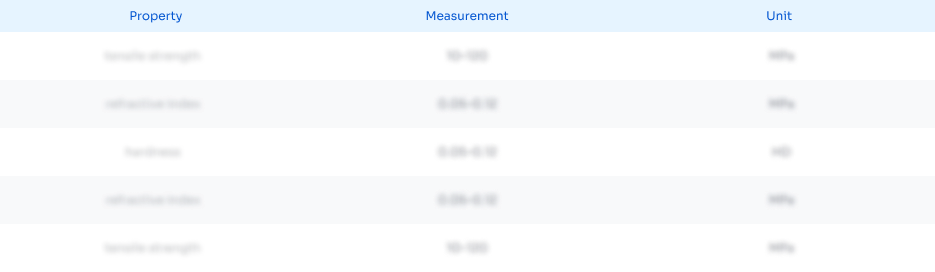
Abstract
Description
Claims
Application Information

- Generate Ideas
- Intellectual Property
- Life Sciences
- Materials
- Tech Scout
- Unparalleled Data Quality
- Higher Quality Content
- 60% Fewer Hallucinations
Browse by: Latest US Patents, China's latest patents, Technical Efficacy Thesaurus, Application Domain, Technology Topic, Popular Technical Reports.
© 2025 PatSnap. All rights reserved.Legal|Privacy policy|Modern Slavery Act Transparency Statement|Sitemap|About US| Contact US: help@patsnap.com