Metal fiber polyporous material subsequent processing method
A technology of porous materials and metal fibers, which is applied in the field of high-precision wire cutting processing, can solve the problems of blocking material pores and polluting materials, and achieves the effects of low cost, simple operation, integrity and stability
- Summary
- Abstract
- Description
- Claims
- Application Information
AI Technical Summary
Problems solved by technology
Method used
Examples
Embodiment Construction
[0009] The present invention will be further described below in conjunction with embodiment.
[0010] The first step is to prepare at least one metal fiber porous material.
[0011] Metal fibers of any material may be used to make metal fiber materials, such as stainless steel, aluminum and aluminum alloys, copper and copper alloy fibers, and the like. The metal fiber can be produced by any known metal fiber production method, such as cluster drawing method, or cutting method and the like. The porosity of the metal fiber porous material can vary widely, with a preferred porosity greater than 70%. The term "porosity" P should be understood as: P = 100 x (1-d).
[0012] Wherein, d=(weight of 1 cubic meter of metal fiber layer) / (SF), SF=weight of dense matrix metal per cubic meter.
[0013] The second step is to fill the pores of the metal fiber porous material with paraffin wax.
[0014] Solid paraffin is preferably ordinary section paraffin. First, the solid paraffin is he...
PUM
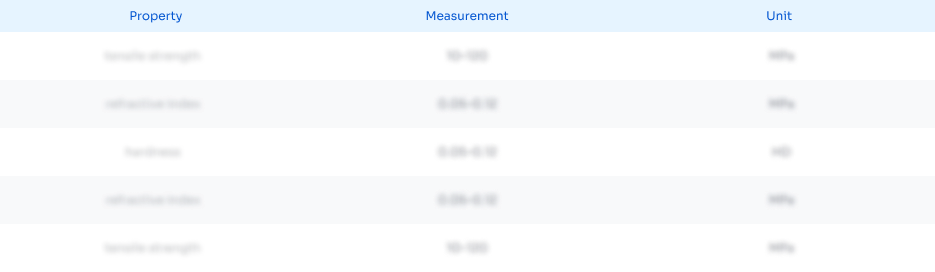
Abstract
Description
Claims
Application Information

- R&D
- Intellectual Property
- Life Sciences
- Materials
- Tech Scout
- Unparalleled Data Quality
- Higher Quality Content
- 60% Fewer Hallucinations
Browse by: Latest US Patents, China's latest patents, Technical Efficacy Thesaurus, Application Domain, Technology Topic, Popular Technical Reports.
© 2025 PatSnap. All rights reserved.Legal|Privacy policy|Modern Slavery Act Transparency Statement|Sitemap|About US| Contact US: help@patsnap.com