Method for producing electrolytic zinc from zinc material with high-content of fluorin and silicon dioxide
A technology of silicon dioxide and electrolytic zinc, which is applied to the improvement of process efficiency, photographic technology, instruments, etc., to achieve the effects of comprehensive utilization, recycling, and reduction of environmental pollution
- Summary
- Abstract
- Description
- Claims
- Application Information
AI Technical Summary
Problems solved by technology
Method used
Examples
Embodiment 1
[0054] Using raw materials containing 56% zinc, 4.17% fluorine, and 0.101% silicon dioxide, the electrolytic waste liquid produced by electrolytic zinc was leached, concentrated and settled, and a neutral zinc sulfate solution containing 155g / l of zinc was obtained. The fluorine solution contains 5.7g / l. In a mechanically stirred tank, the temperature is controlled at 20-60°C and the pH value is 2.0-5.0. Add powdered silicon dioxide at 20g / l and potassium sulfate at 8.7g / l to control The flow rate is continuously produced, the reaction time is 30-60 minutes, and then pumped into the box-type filter press for pressure filtration to obtain potassium fluorosilicate residue. The filtered solution is added with powdered calcium sulfate at 3.3g / l, and stirred for 40 minutes. After adding zinc powder to remove other impurities such as copper, cadmium, and cobalt, the obtained Zinc sulfate solution less than 0.0001g / l, through electrolysis process to produce cathode zinc flakes.
Embodiment 2
[0056]Use raw materials containing 56% zinc and 4.17% fluorine and raw materials containing 53% zinc and 7.0% silicon dioxide to mix according to the ratio of 1:1.8, and then use the electrolytic waste liquid produced by electrolytic zinc to leach, concentrate and settle, Prepare a neutral zinc sulfate solution containing 152g / l of zinc. In a mechanically stirred tank, control the temperature at 20-60°C, add potassium sulfate at 3.1g / l, control the flow rate for continuous production, and use the reaction time for 30-60 minutes. Put the pump into the box-type filter press and filter to obtain potassium fluorosilicate residue. Add powdered calcium sulfate to the filtered liquid at a rate of 3.3g / l, stir for 40 minutes, and add zinc powder to remove other impurities such as copper, cadmium, and cobalt. Finally, a zinc sulfate solution containing 153g / l of zinc, less than 0.0002g / l of copper, less than 0.0005g / l of cadmium, less than 0.001g / l of cobalt, 0.031g / l of fluorine, and l...
PUM
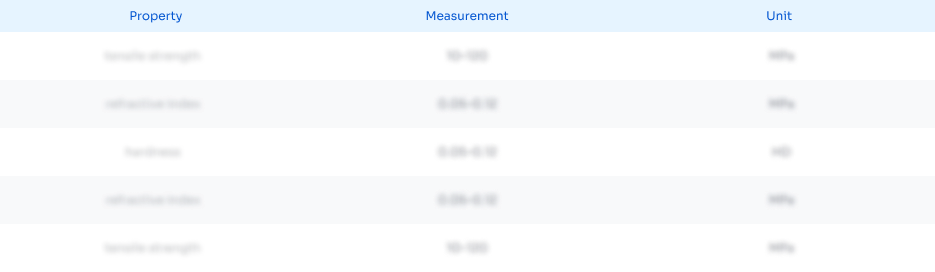
Abstract
Description
Claims
Application Information

- R&D Engineer
- R&D Manager
- IP Professional
- Industry Leading Data Capabilities
- Powerful AI technology
- Patent DNA Extraction
Browse by: Latest US Patents, China's latest patents, Technical Efficacy Thesaurus, Application Domain, Technology Topic, Popular Technical Reports.
© 2024 PatSnap. All rights reserved.Legal|Privacy policy|Modern Slavery Act Transparency Statement|Sitemap|About US| Contact US: help@patsnap.com