Method for manufacturing lactide with polyhydroxy lactic acid oligomer
A polyhydroxylactic acid, lactide technology, applied in the direction of organic chemistry, etc., can solve problems such as hindering the normal progress of the degradation reaction
- Summary
- Abstract
- Description
- Claims
- Application Information
AI Technical Summary
Problems solved by technology
Method used
Image
Examples
Embodiment 1
[0021] Add 68g of L-lactic acid (88% aqueous solution), 1.2g of 1,4-butanediol and 0.3g of stannous octoate into a three-necked bottle equipped with mechanical stirring, place it in an oil bath at 100°C, and slowly evacuate to 40mmHg, water evaporates, maintain the vacuum state, gradually raise the temperature to 180°C, react for 6 hours, the molecular weight can reach 6600. The heating mantle was changed and the temperature was raised to 220° C., and the vacuum was pumped to 3 mmHg. The pyrolysis reaction was completed in 40 minutes, and 46 g of crude lactide was collected, with a yield of 93%.
Embodiment 2
[0023] Add 100g of D,L-lactic acid (85% aqueous solution), 2.4g of 1,3-propanediol and 0.7g of stannous chloride into a three-necked bottle equipped with mechanical stirring, place it in an oil bath at 100°C, and slowly evacuate When it reached 70mmHg, some water evaporated, and the vacuum state was maintained, and the temperature was gradually raised to 180°C, and the reaction was carried out for 8 hours, and the molecular weight could reach 3800. Replace the heating mantle and raise the temperature to 220° C., vacuumize to 4 mmHg, and the thermal cracking reaction ends in about 1 hour. 61 g of light yellow crude lactide is collected, with a yield of 90%.
Embodiment 3
[0025] Add 100g of L-lactic acid (88% aqueous solution), 0.8g of ethylene glycol and 0.6g of zinc oxide into a three-necked bottle equipped with mechanical stirring, place it in an oil bath at 100°C, and slowly evacuate to 40mmHg, and some water will evaporate , maintain the vacuum state, gradually raise the temperature to 180°C, react for 8 hours, and the molecular weight can reach 10500. Replace the heating mantle and raise the temperature to 220° C., vacuumize to 4 mmHg, and the pyrolysis reaction ends in about 1.5 hours. Collect and obtain 59.5 g of pale yellow crude lactide, with a yield of 85%.
PUM
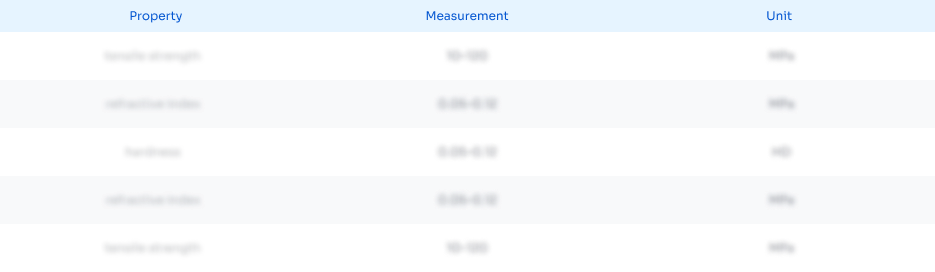
Abstract
Description
Claims
Application Information

- R&D
- Intellectual Property
- Life Sciences
- Materials
- Tech Scout
- Unparalleled Data Quality
- Higher Quality Content
- 60% Fewer Hallucinations
Browse by: Latest US Patents, China's latest patents, Technical Efficacy Thesaurus, Application Domain, Technology Topic, Popular Technical Reports.
© 2025 PatSnap. All rights reserved.Legal|Privacy policy|Modern Slavery Act Transparency Statement|Sitemap|About US| Contact US: help@patsnap.com