High glazing and high liquidity glass fiber-reinforced nylon 6 composite material and preparation method thereof
A glass fiber and composite material technology, applied in the field of high gloss, can solve the problems of loss of material mechanical properties and thermal properties, unmentioned material molding flow properties, rising product cost, etc., to achieve improved mechanical properties, good surface gloss, improved The effect of processability
- Summary
- Abstract
- Description
- Claims
- Application Information
AI Technical Summary
Problems solved by technology
Method used
Examples
Embodiment 1
[0047] The weight ratio of PA6 resin is 84.5%, the weight ratio of glass fiber is 10%, the weight ratio of MAPP is 3%, the weight ratio of KH550 is 0.2%, the weight ratio of 1010 / 168 is 0.1 / 0.2%, and the weight ratio of high-gloss masterbatch A is 2%. , the above components are mixed at room temperature in a high-speed mixer, and produced by a TE-35 (L / D=48) twin-screw extruder produced by Nanjing Keya Company, and its processing temperature (from the feed port to the die) head) are: 170°C, 200°C, 215°C, 220°C, 225°C, the speed of the main engine is 30 Hz, and the test results are listed in Table 1.
Embodiment 2
[0049] The weight ratio of PA6 resin is 74.3%, the weight ratio of glass fiber is 20%, the weight ratio of MAPP is 3%, the weight ratio of KH550 is 0.4%, the weight ratio of 1010 / 168 is 0.1 / 0.2%, and the weight ratio of high-gloss masterbatch A is 2%. , the above components are mixed at room temperature in a high-speed mixer, and produced by a TE-35 (L / D=48) twin-screw extruder produced by Nanjing Keya Company, and its processing temperature (from the feed port to the die) head) are: 180°C, 210°C, 215°C, 220°C, 230°C, the speed of the main engine is 30 Hz, and the test results are listed in Table 1.
Embodiment 3
[0051] The weight ratio of PA6 resin is 62.1%, the weight ratio of glass fiber is 30%, the weight ratio of MAPP is 4%, the weight ratio of KH550 is 0.6%, the weight ratio of 1010 / 168 is 0.1 / 0.2%, and the weight ratio of high-gloss masterbatch A is 3% , the above components are mixed at room temperature in a high-speed mixer, and produced by a TE-35 (L / D=48) twin-screw extruder produced by Nanjing Keya Company, and its processing temperature (from the feed port to the die) head) are: 180°C, 220°C, 225°C, 230°C, 240°C, the speed of the main engine is 30 Hz, and the test results are listed in Table 1.
PUM
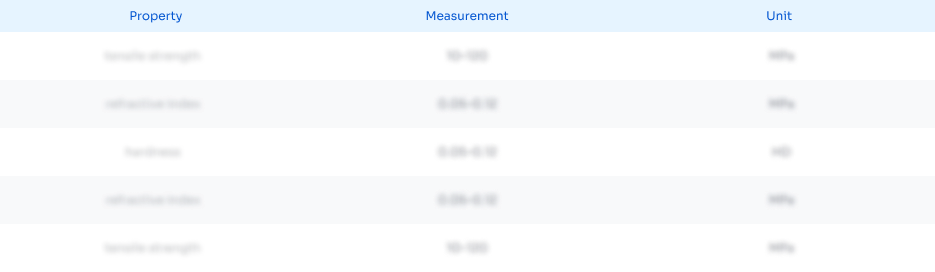
Abstract
Description
Claims
Application Information

- R&D Engineer
- R&D Manager
- IP Professional
- Industry Leading Data Capabilities
- Powerful AI technology
- Patent DNA Extraction
Browse by: Latest US Patents, China's latest patents, Technical Efficacy Thesaurus, Application Domain, Technology Topic, Popular Technical Reports.
© 2024 PatSnap. All rights reserved.Legal|Privacy policy|Modern Slavery Act Transparency Statement|Sitemap|About US| Contact US: help@patsnap.com