Strip steel continuous zinc heat coating process
A process method, hot-dip galvanizing technology, which is applied in the direction of hot-dip galvanizing process, process efficiency improvement, metal material coating process, etc., can solve the problem that the strip steel surface grease and oxide scale cannot be removed, and achieve the elimination of combustion and explosion hazards , reduce tension and reduce cost
- Summary
- Abstract
- Description
- Claims
- Application Information
AI Technical Summary
Problems solved by technology
Method used
Image
Examples
Embodiment Construction
[0028] A process method for strip steel continuous hot-dip galvanizing, as shown in Figure 1, it comprises:
[0029] The first cleaning step: for cleaning and removing residues on the surface of the strip;
[0030] Alkali cleaning step: for removing the grease on the strip surface, the solution used in this alkali cleaning step is 15% sodium hydroxide solution, the solution used in this embodiment is sodium hydroxide solution, but not using sodium hydroxide solution as Limit, can also use sodium hydroxide, sodium silicate, sodium phosphate, sodium carbonate mixture, etc.;
[0031] Pickling step: used to remove scale and reaction products on the surface of the steel strip. The solution used in this pickling step is a hydrochloric acid solution. The solution used in this embodiment is a hydrochloric acid solution, but it is not limited to the hydrochloric acid solution. Using sulfuric acid, etc.;
[0032] The second cleaning step: for cleaning and removing the products of alka...
PUM
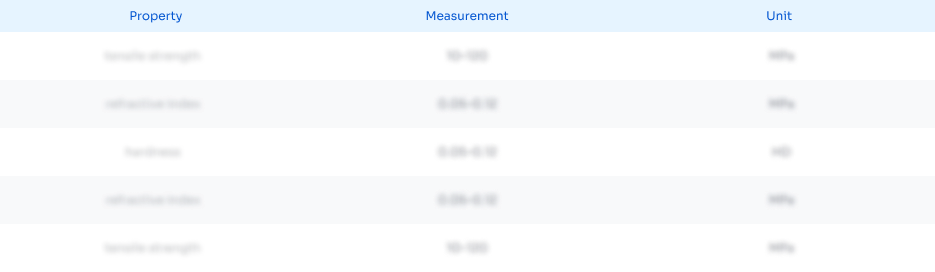
Abstract
Description
Claims
Application Information

- R&D
- Intellectual Property
- Life Sciences
- Materials
- Tech Scout
- Unparalleled Data Quality
- Higher Quality Content
- 60% Fewer Hallucinations
Browse by: Latest US Patents, China's latest patents, Technical Efficacy Thesaurus, Application Domain, Technology Topic, Popular Technical Reports.
© 2025 PatSnap. All rights reserved.Legal|Privacy policy|Modern Slavery Act Transparency Statement|Sitemap|About US| Contact US: help@patsnap.com